It was always expecting I would have to make some replacement Bolection Moulds for the beautiful old antique door which I had been restoring. The story continues to unfold...
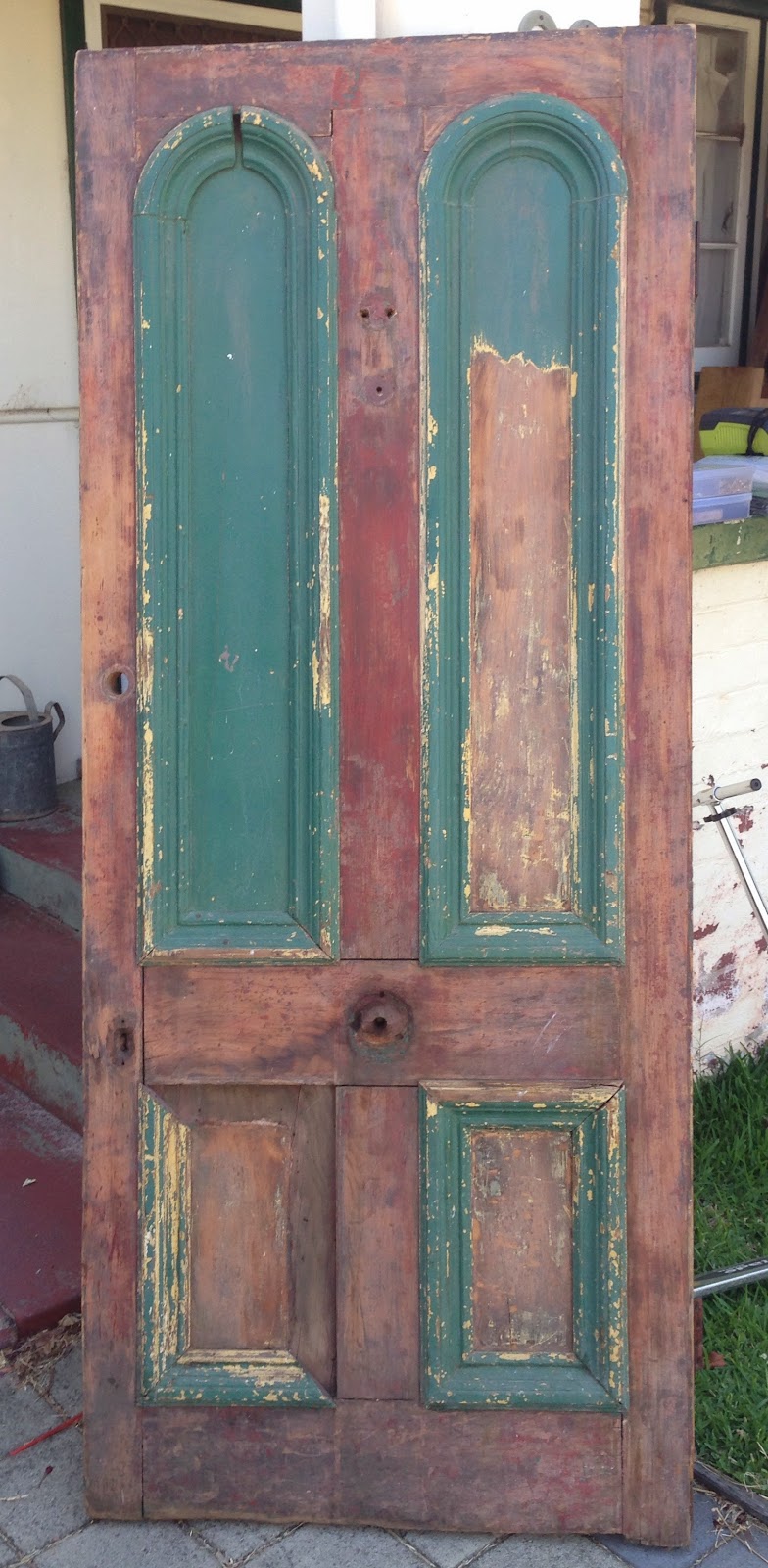 |
The starting point... a century old door in need of some attention. |
Firstly, in
Part One, I assessed the door to work out what needed to be done.
Then in
Part Two, I pulled the door's frame and panels apart and then re-built it.
Now, in this third part of the saga, the bolection moulds will be repaired and affixed to the face of the door as the top panels are prepared for the addition of leadlight windows, replacing the arched timber panels. Such a challenge and privilege to have the responsibility of breathing new life into this door!
Matching the profile to make more mouldings.
Below thick layers of old paint, the bolection moulds have a complicated profile. My task was to make new mouldings to replace the missing or damaged sections. The starting point was to work out the geometry of the original mouldings so that I could make new moulding sections as close a match as possible.
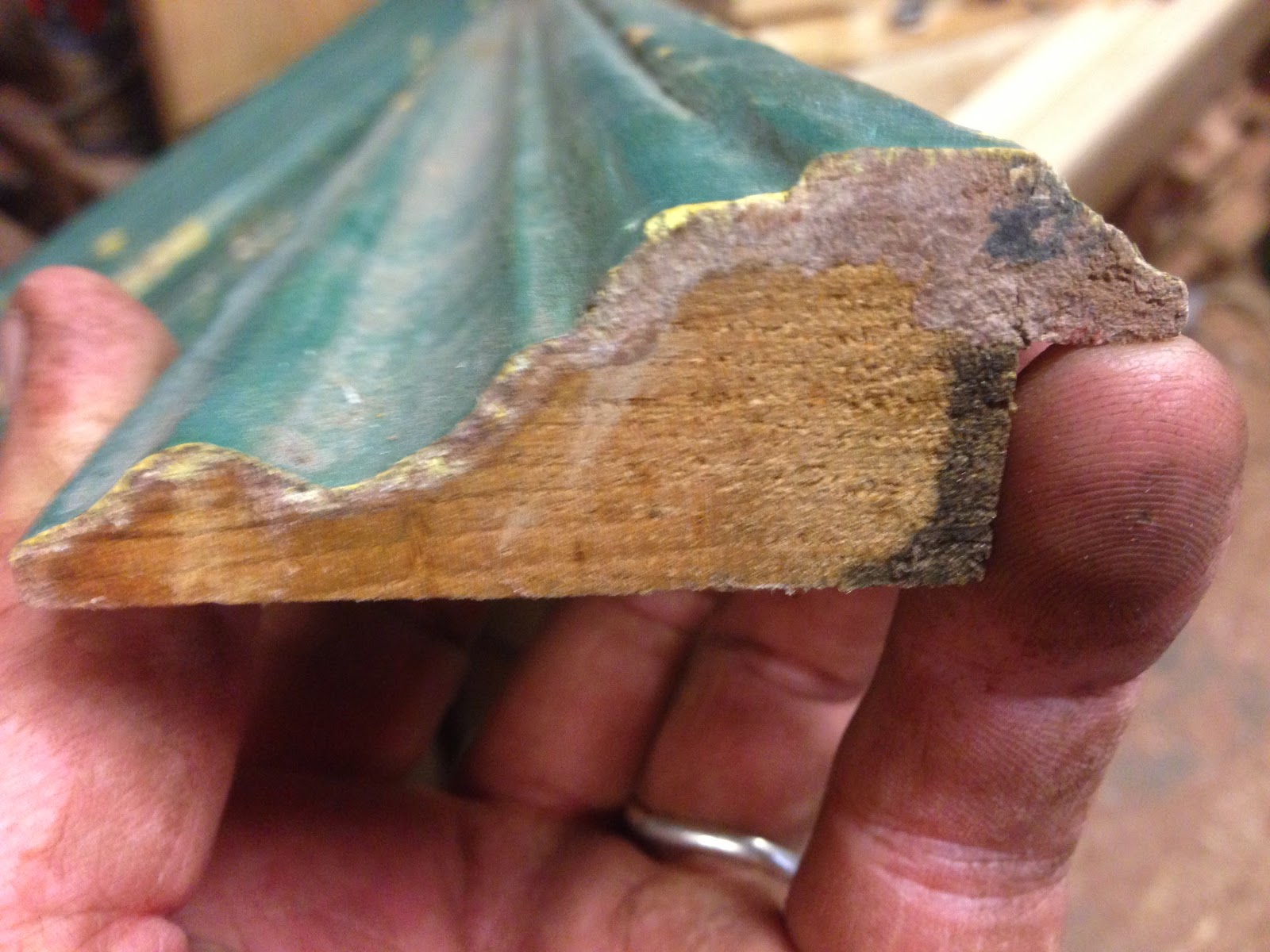 |
Under the paint lies some interesting geometry. I had to match it. |
The best way to match these is with the old wooden moulding planes, Hollows and Rounds. I have a heap of these which I have been gathering up over the last 6 years. Many are waiting to be cleaned up and put back into service, but I tend to do this as I need them. Time to open up my 4 boxes of moulding planes...
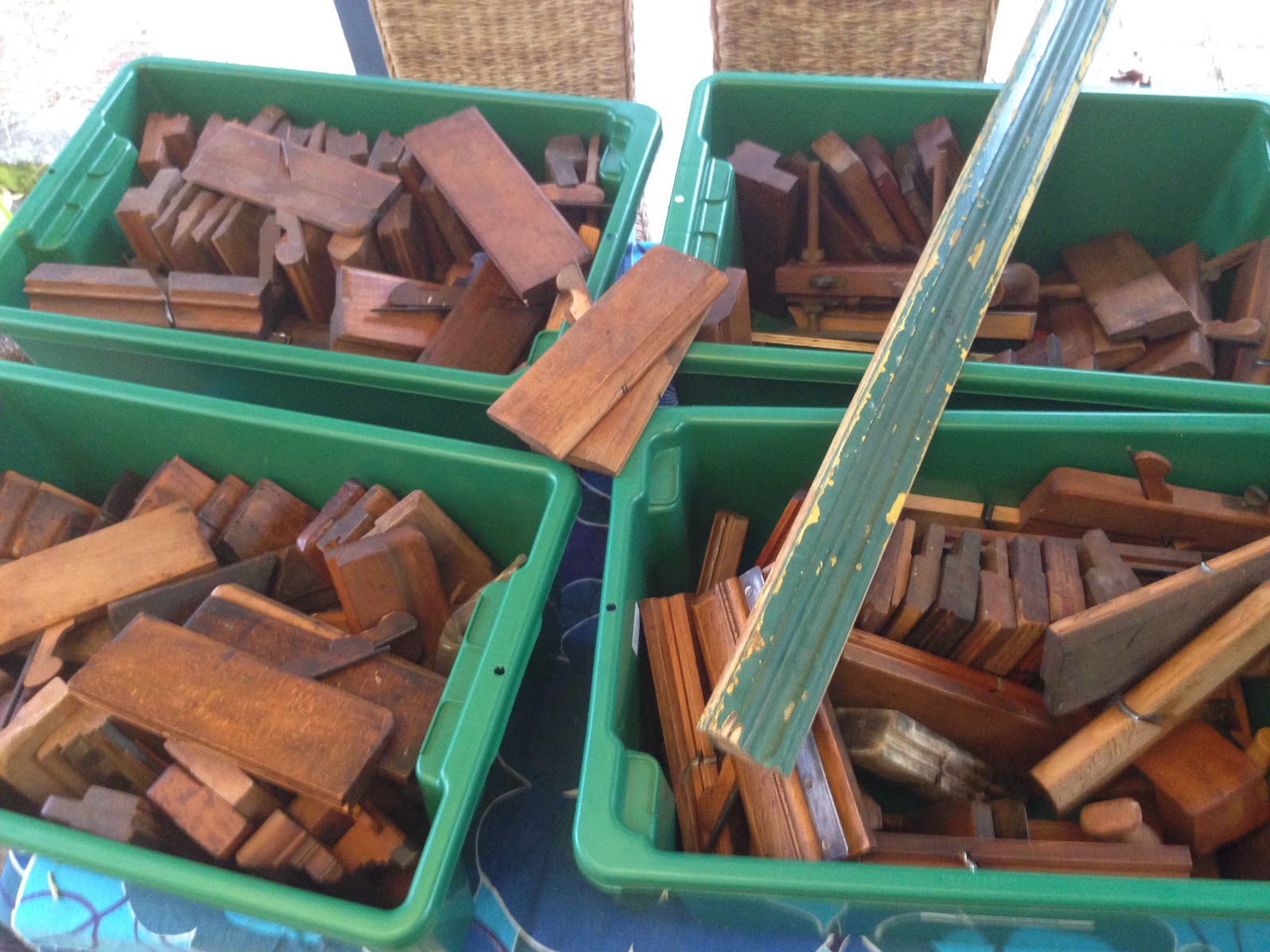 |
Choose your weapons! |
I was looking for the right radii on the hollows and rounds.
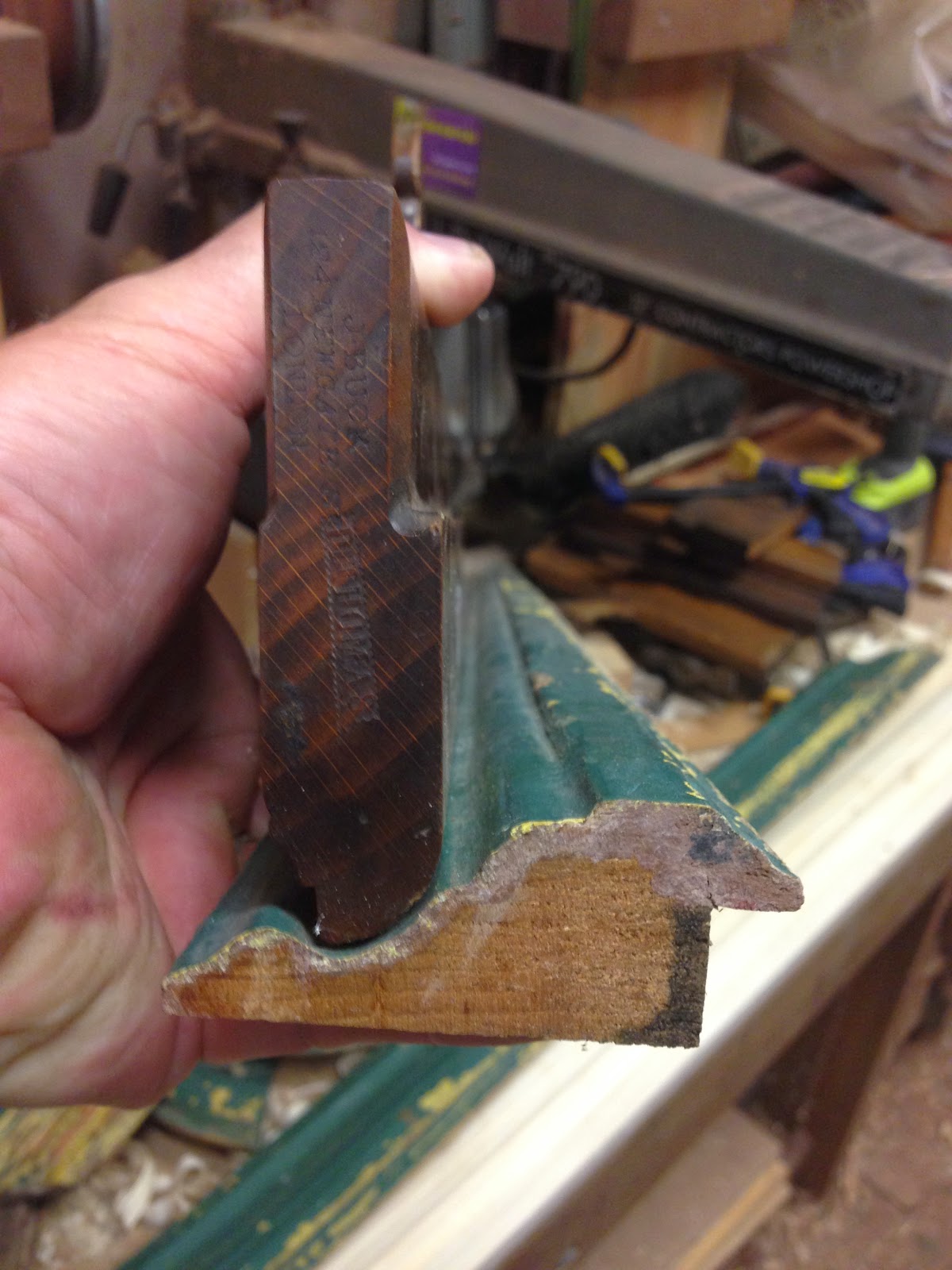 |
This "Half-Round" plane is a winner on this section. |
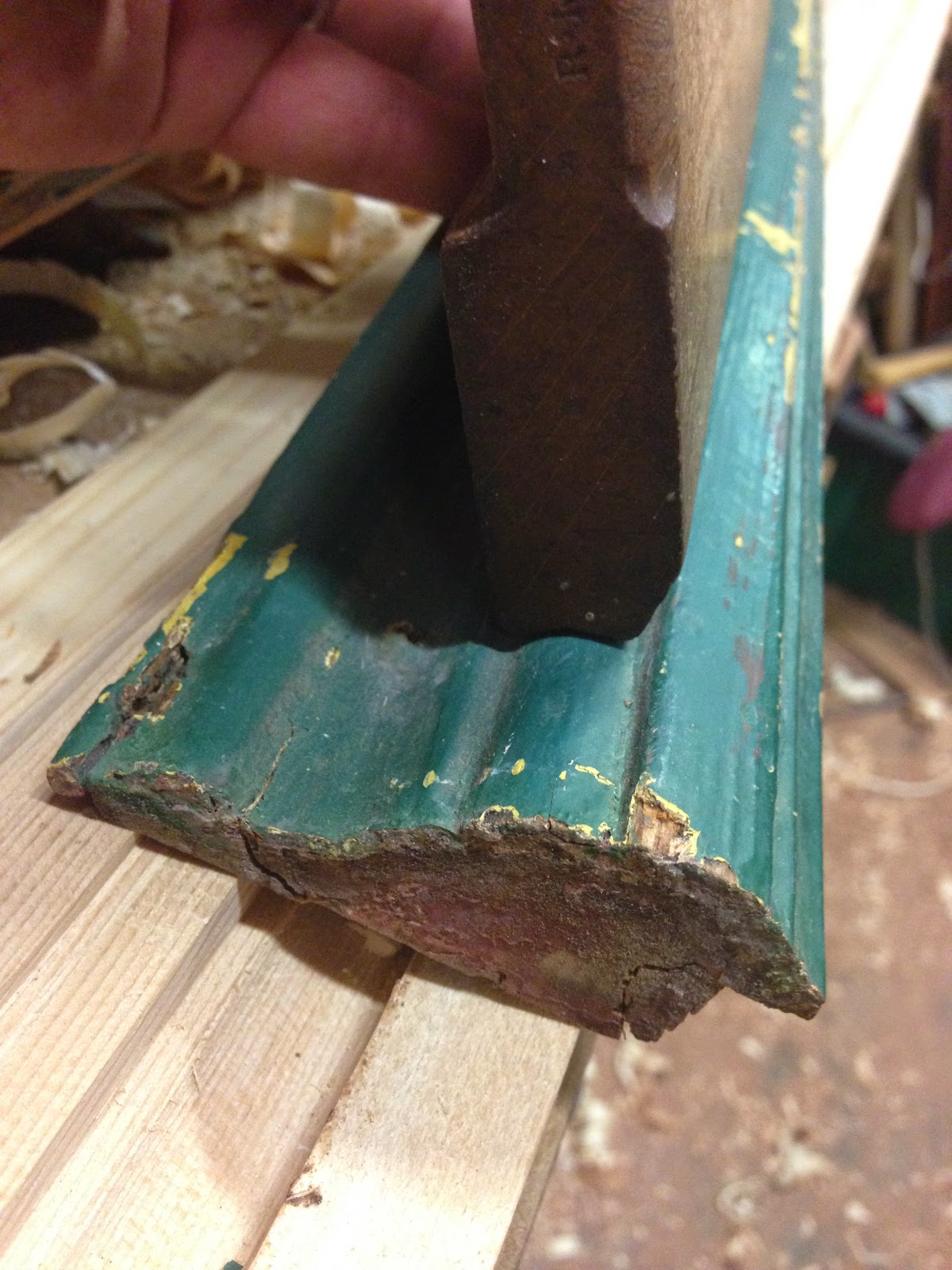 |
This Hollow is a winner too. |
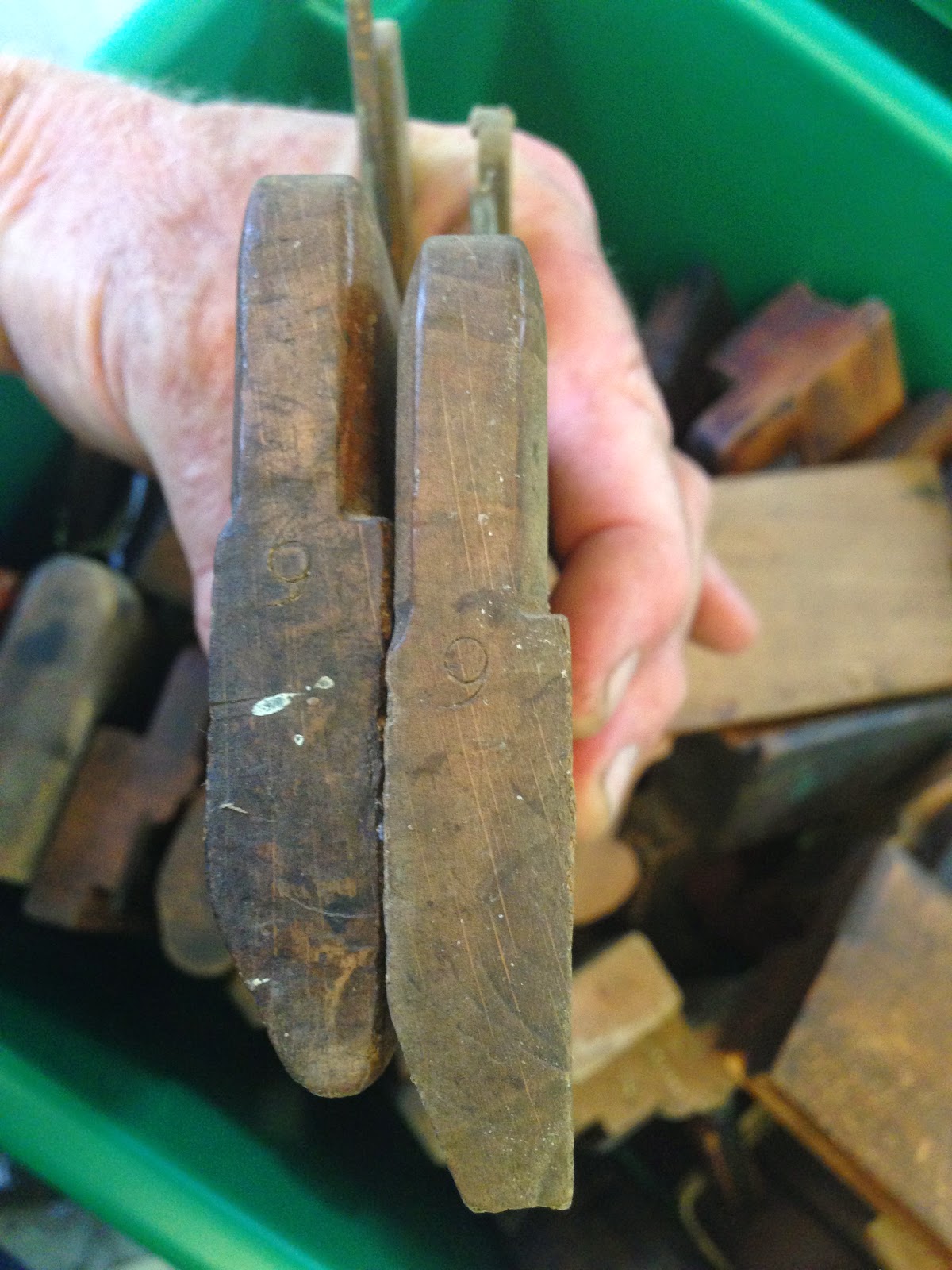 |
Another pair of Hollows and Rounds are a good fit too. |
With the right combination of moulding planes selected, it was time to tackle the making of the mouldings.
The essential thing to understand regarding the use of moulding planes is laying the foundations first - the rebates and chamfers. The best book on this subject that I have come across was published a couple of years ago, by
Lost Art Press in the USA.
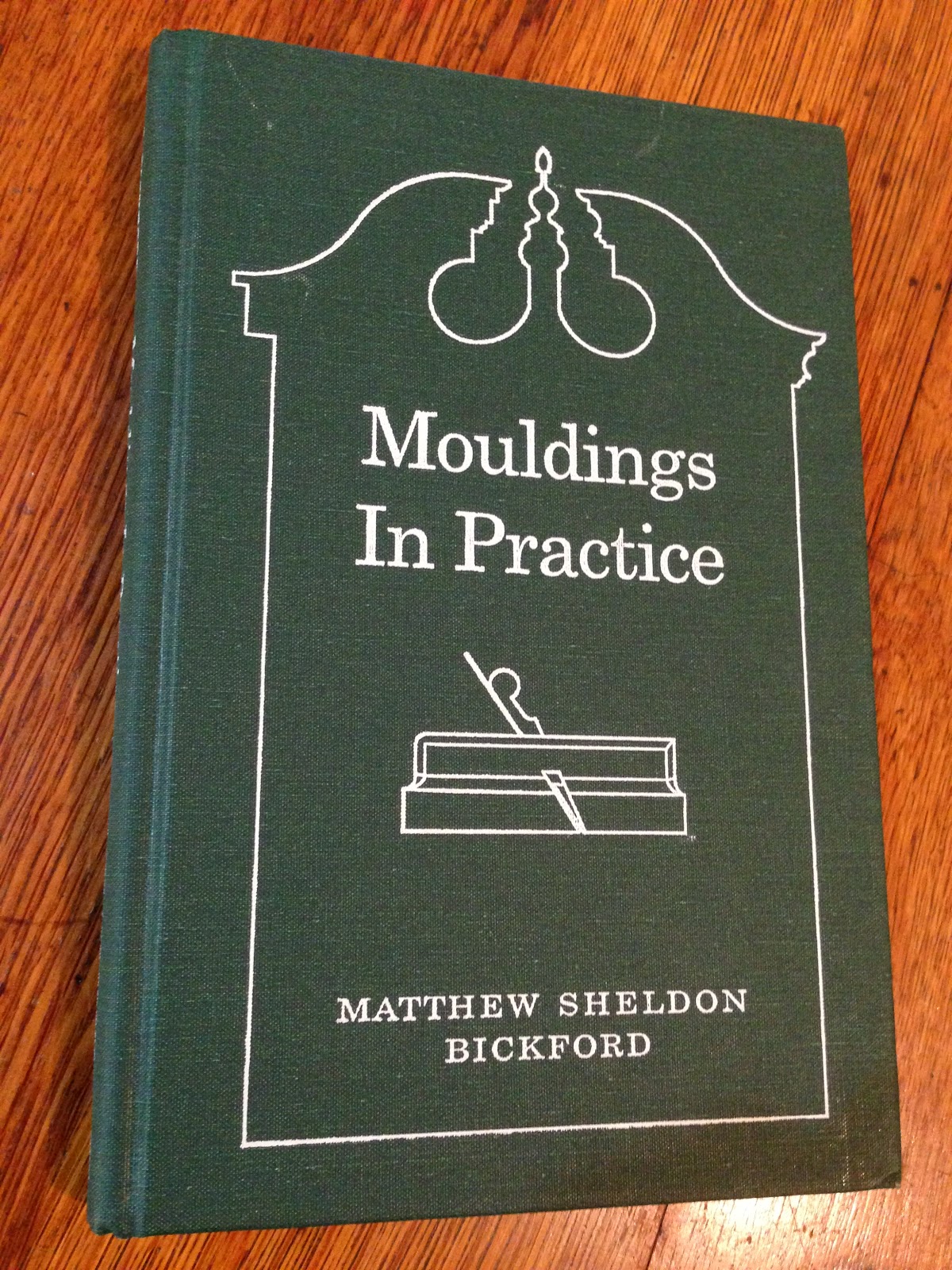 |
Matt Bickford, you are a legend. This book is brilliant. |
Reading this book turned the lights on for me at the time. It made a lot of sense. The most important principle Bickford makes clear regards the laying down the foundational rebates and chamfers first. This facilitates consistency as well as saving the cutting edges of the moulding planes from unnecessary wear - they are tricky to sharpen!
I started by machining the timber to the required starting point - 76mm x 22mm (3" x 7/8"). I used a router cutter to cut one small Roman Ogee profile, and then machined a series of rebates and shoulders over the table saw.
Sure, it's nicer to do the rebates with a nice wooden rebate or moving filister plane, but I owe it to my customer to do it in the shortest time possible, as she was paying by the hour. Hence the table saw solution for much of the foundational work. Now it was time for the fun part...
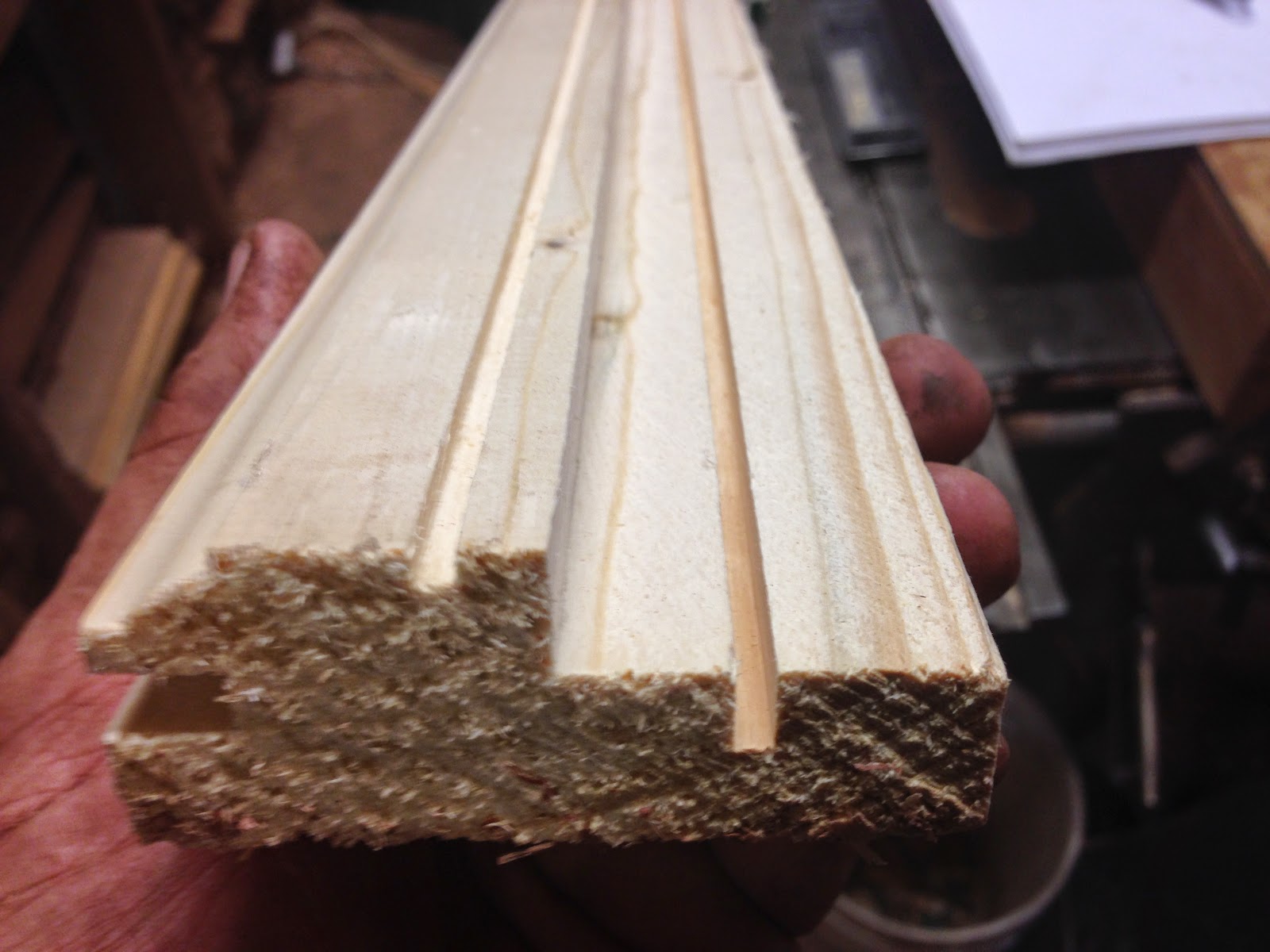 |
Laying the foundations for the moulding planes. |
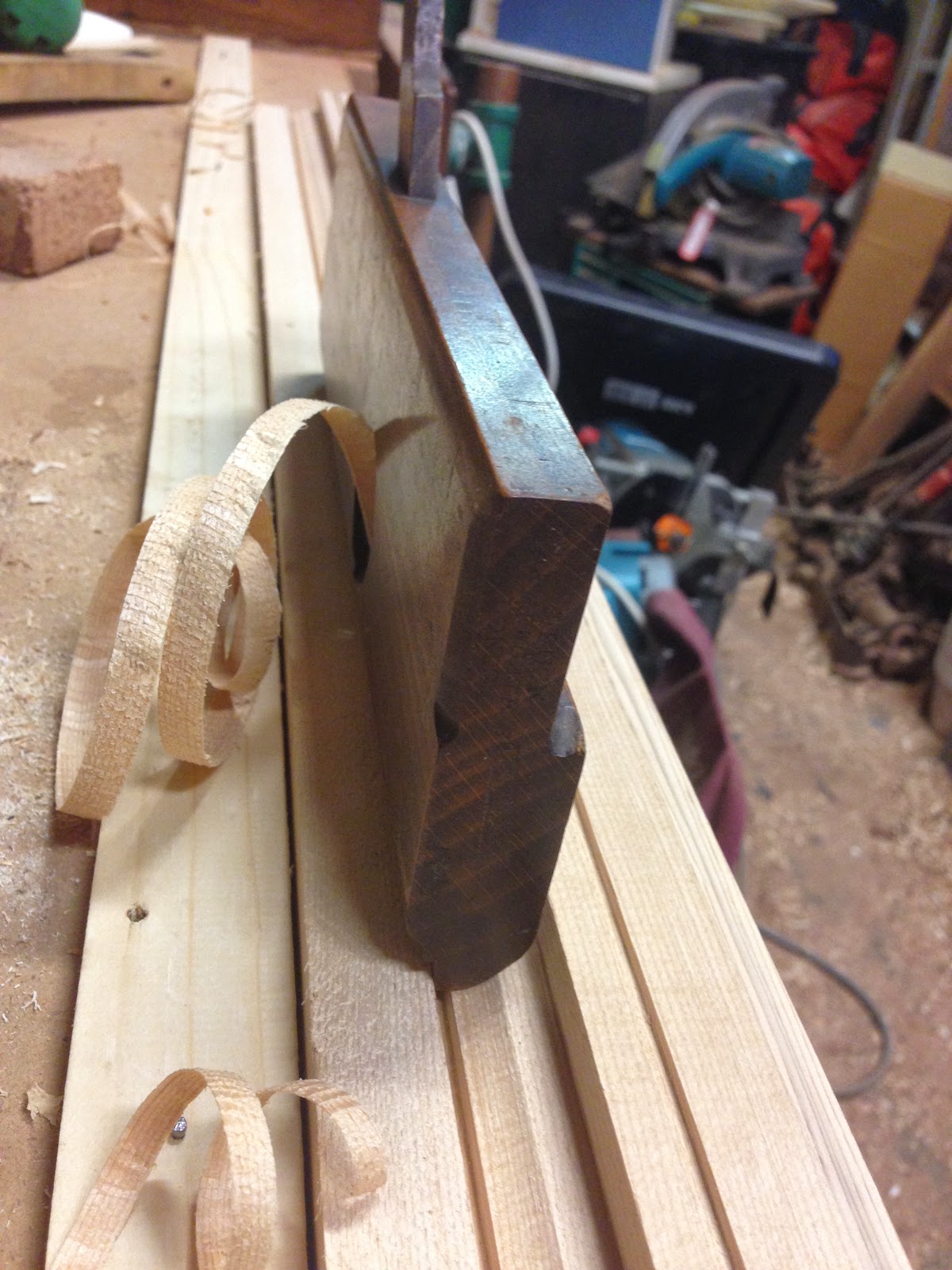 |
The Half Round Plane cuts the nice rising curve against the vertical shoulder. |
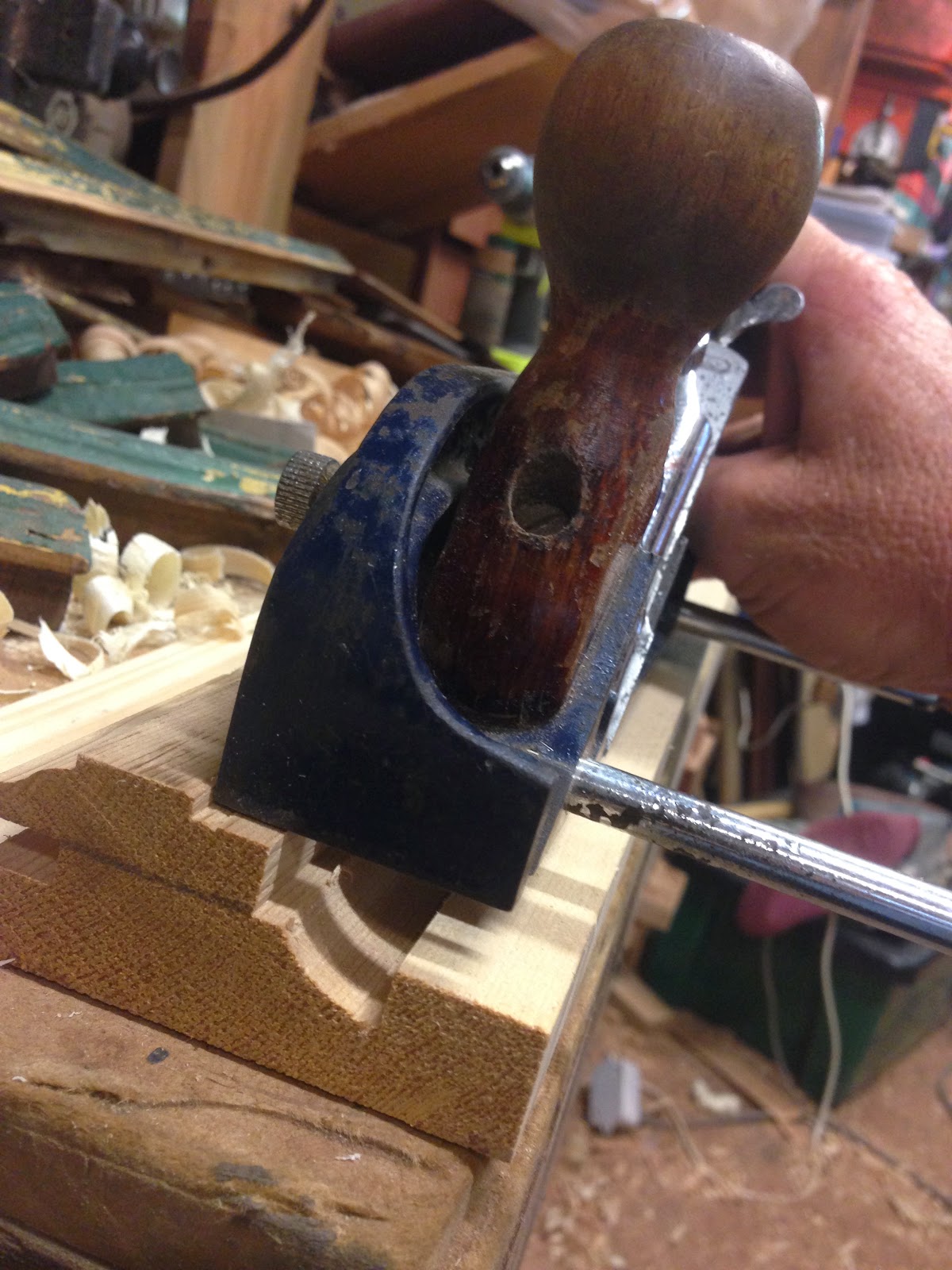 |
Using the No78 Rebate Plane to complete a shoulder. |
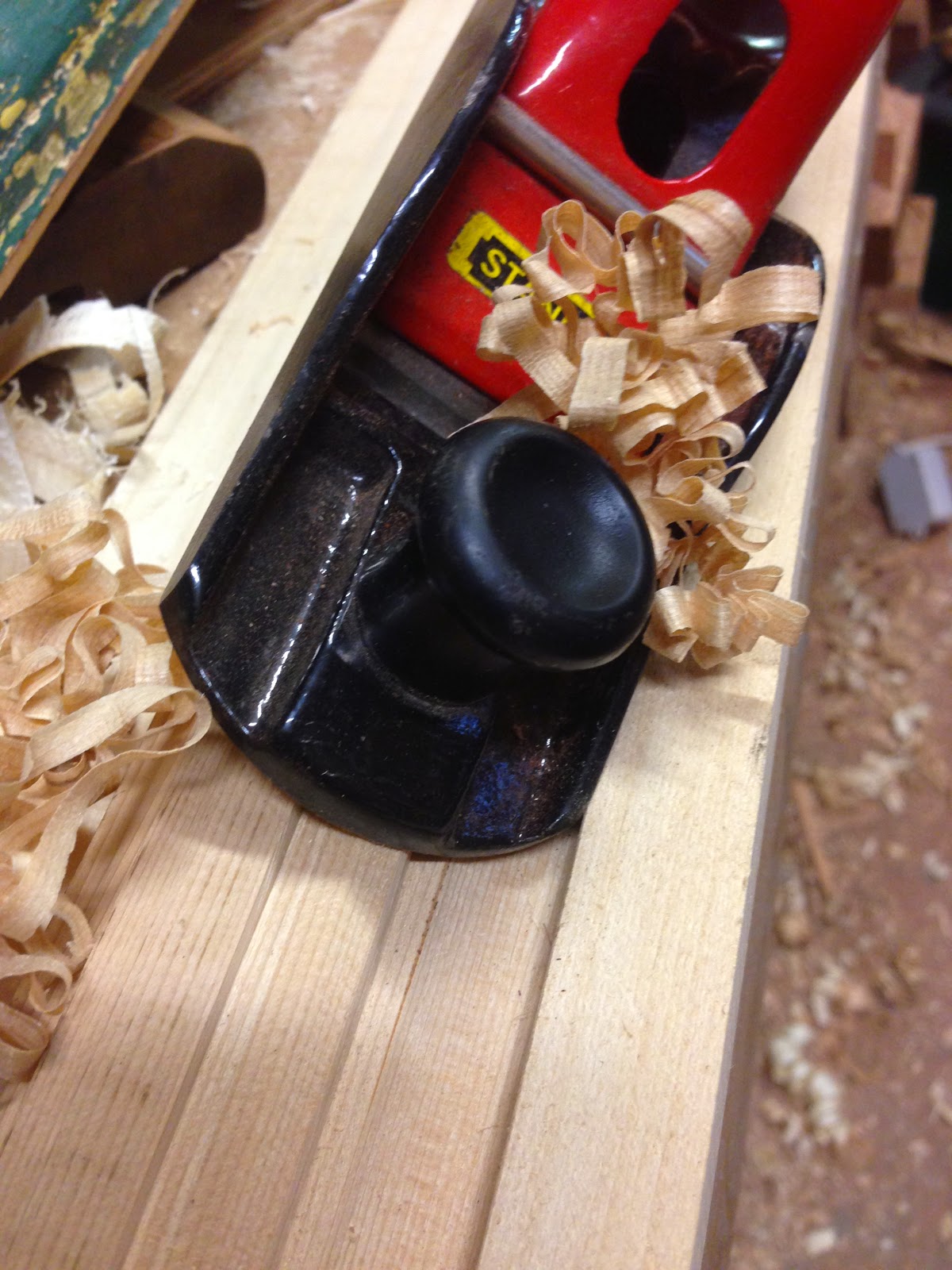 |
The Blockplane creates s chamfer ready to create an Ovolo. |
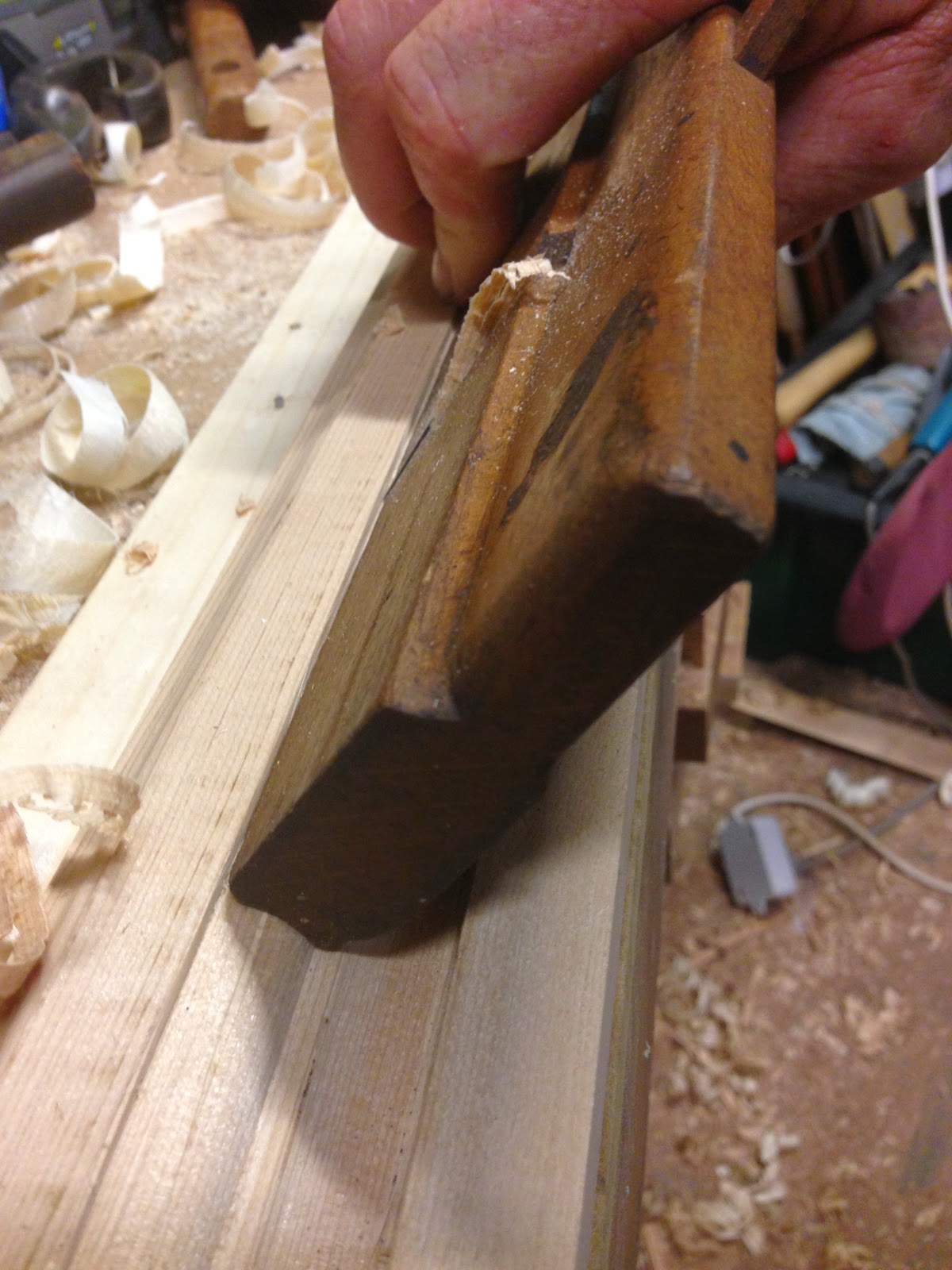 |
Using the right radius Hollow Plane to create the Ovolo with a quirk on each side. |
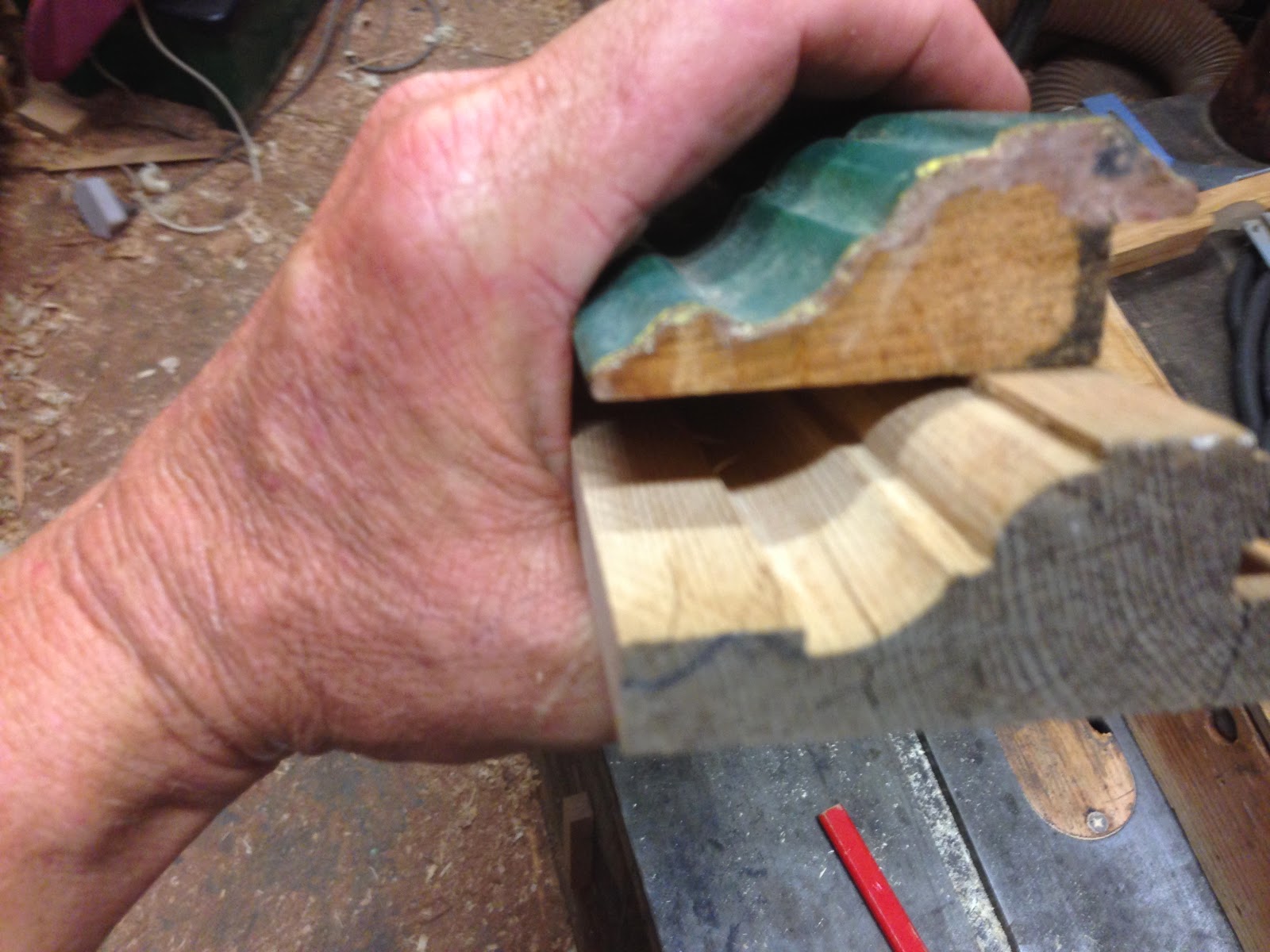 |
Progress check thus far... looking good! |
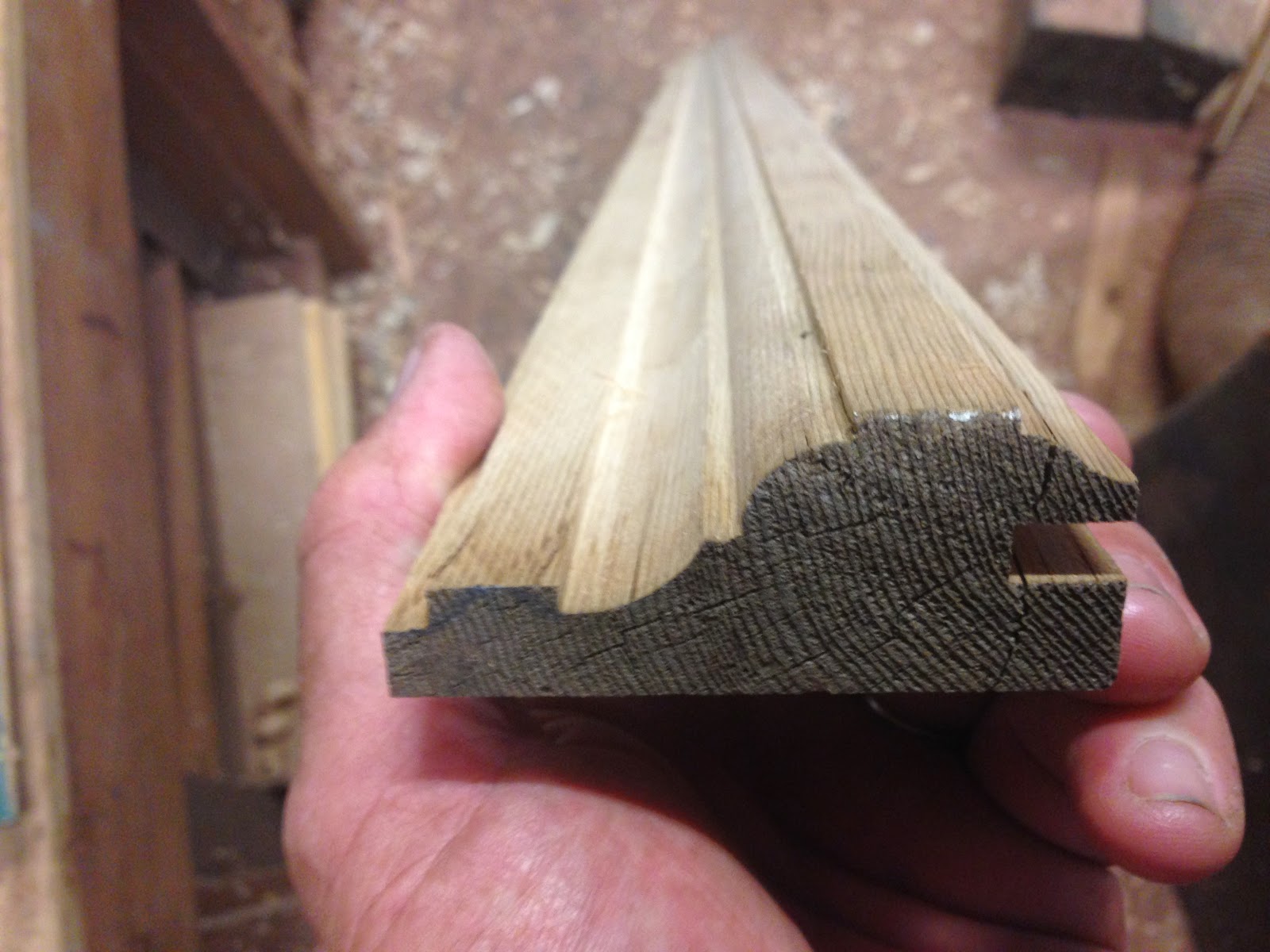 |
Rebate cut along the lower LH edge ready for the next profile. |
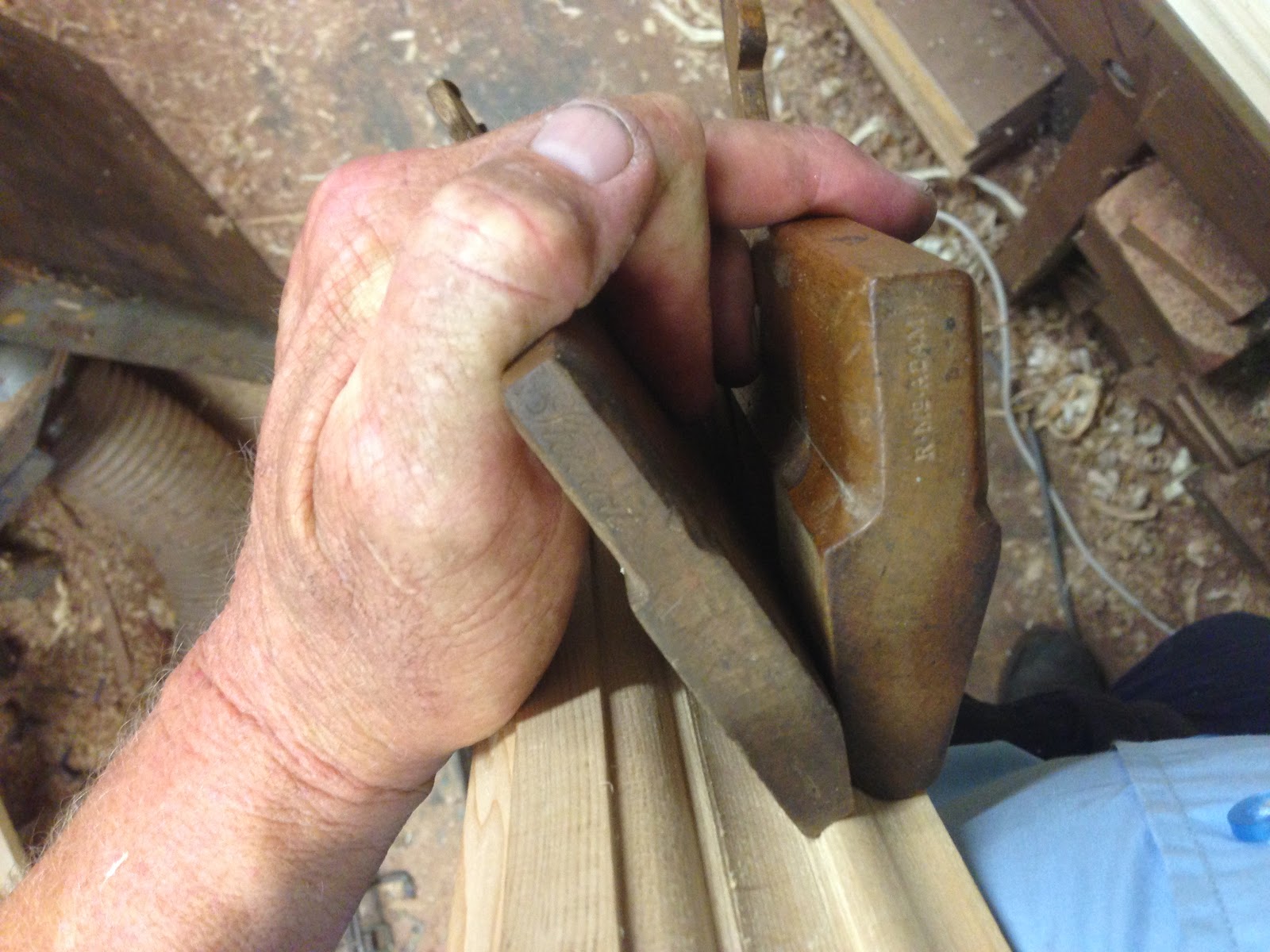 |
Combination of Hollow and Round to shape the lower Ogee. |
Fitting the mouldings to the front side of the door.
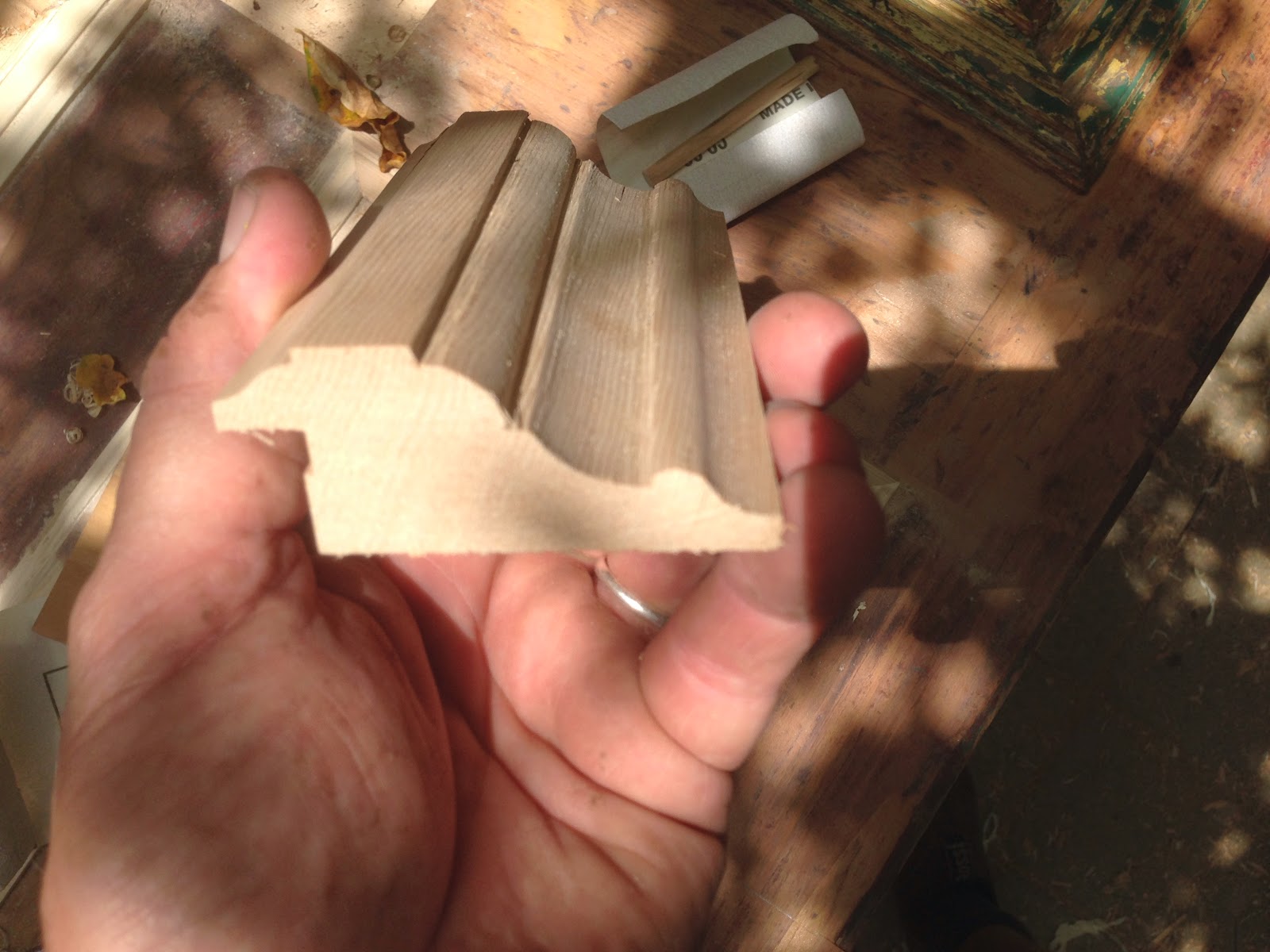 |
Done. Rough enough, eh? |
With some sections of mouldings run, it was back to the door...
 |
Front side: new lower mouldings fitted. Now laying out the old top mouldings. |
With the lower mouldings fitted on the front side, it was time to tackle the top mouldings. A couple of the long pieces were in very bad shape, so the better original sections from the lower mouldings were re-cut with scarf joints to replace these dodgy parts.
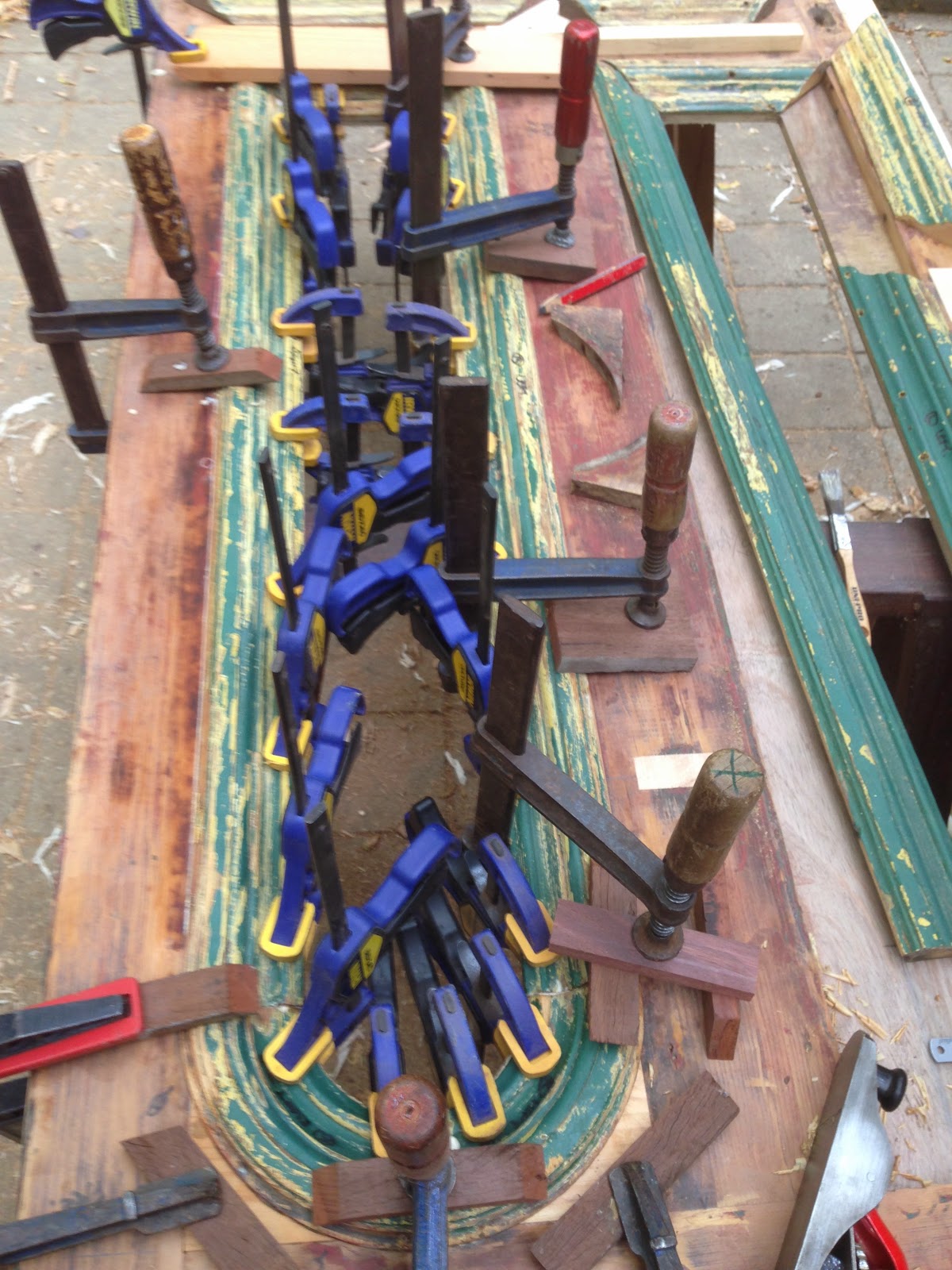 |
Gluing down the mouldings to the shaped marine ply panel. |
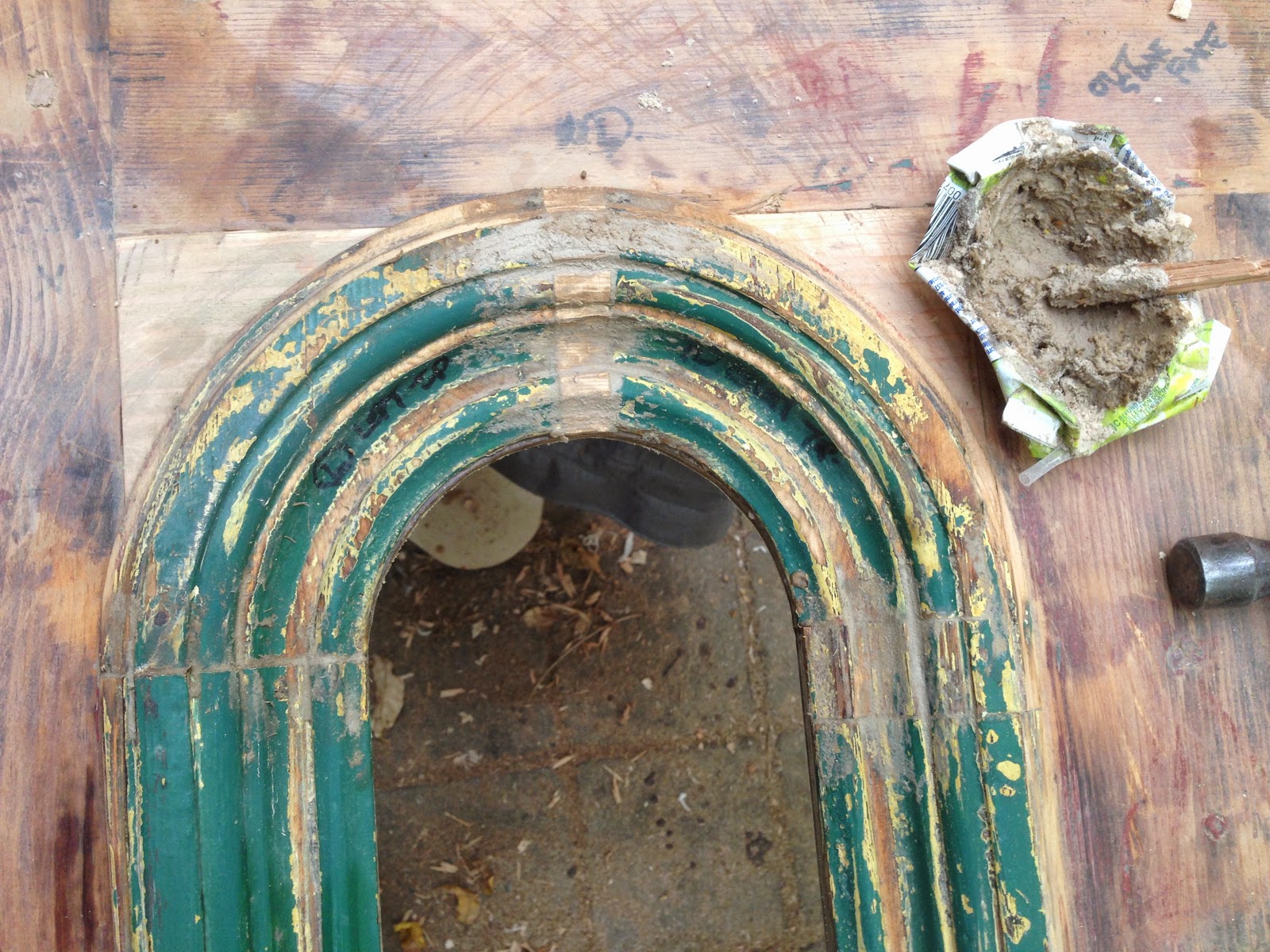 |
The missing centre piece replaced, and a glue/sawdust mix used to fill small holes around the arch. |
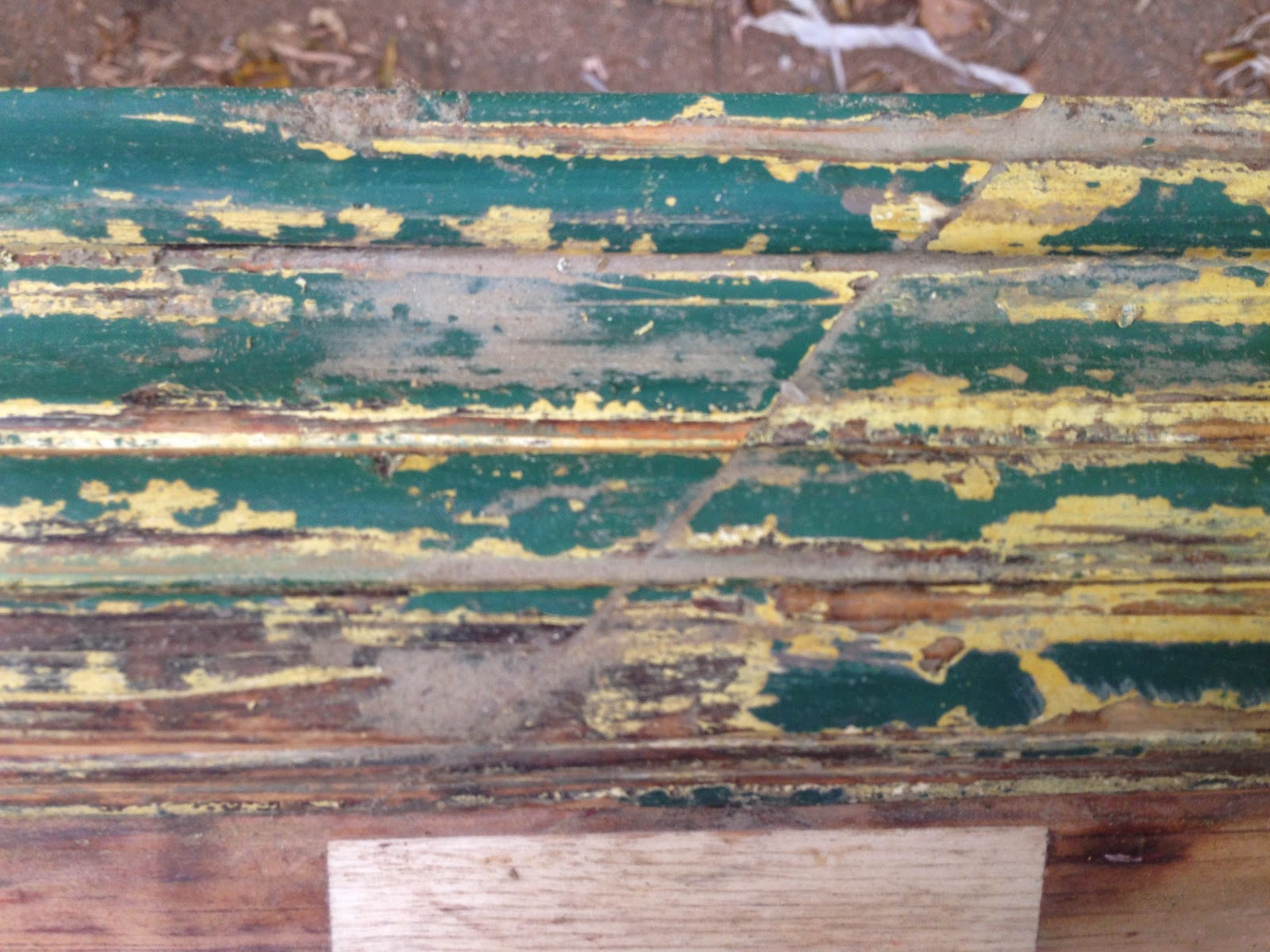 |
Discrete scarf joints join various good sections together to create the long top sections. |
So why the marine ply panel? The original Western Red Cedar panels were pretty cactus - especially the bottom panels. Badly weathered, split and damaged. So the original two top panels were cut down to replace the original bottom panels, and new top panels were made from marine ply. With the top panels being modified to house leadlights now, and many of he original mouldings being damaged along the inside edges, a way had to be made to house the leadlights solidly in a rebate under the front bolection mould edges.
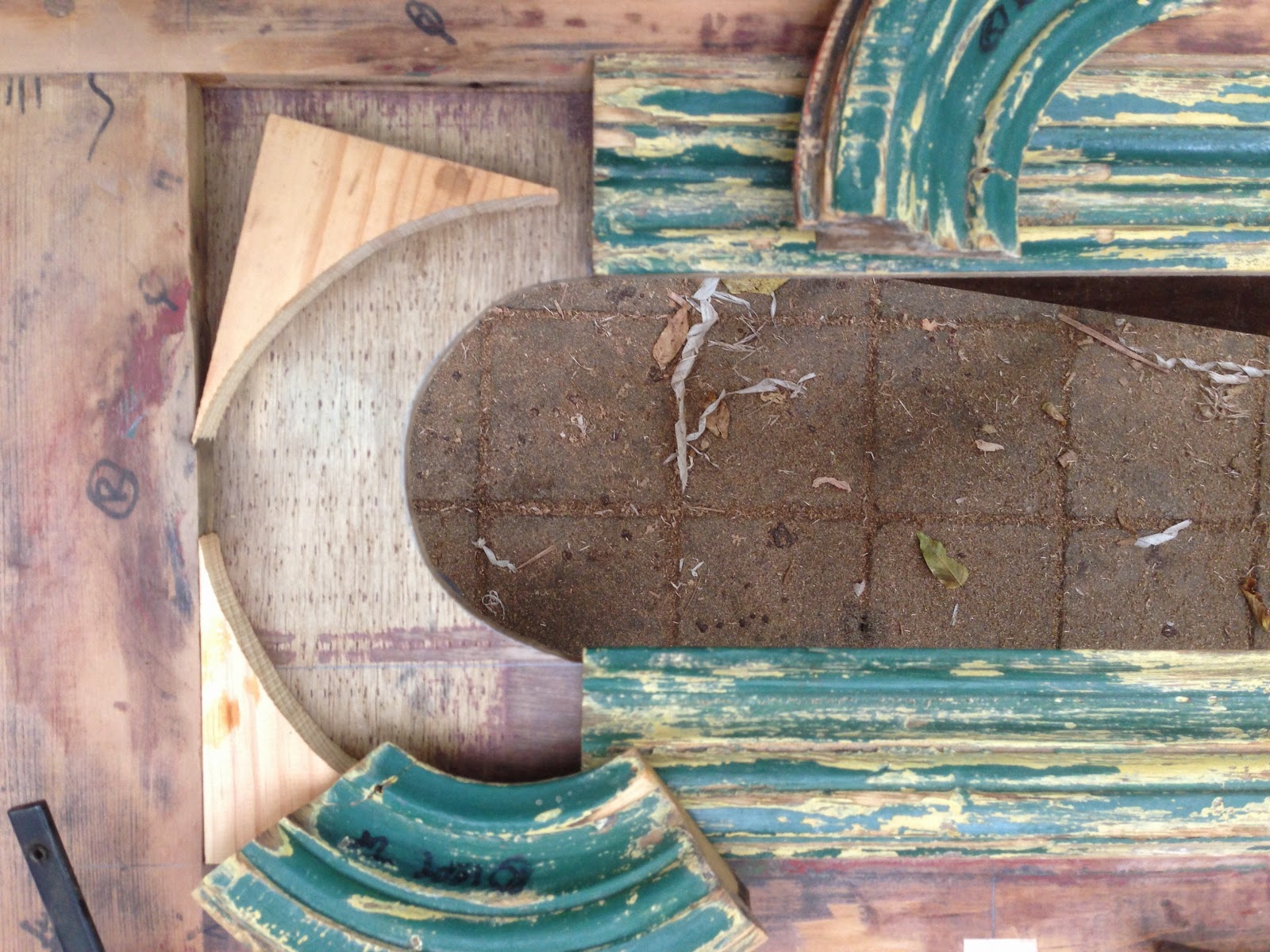 |
Checking all the pieces before gluing and nailing in place. |
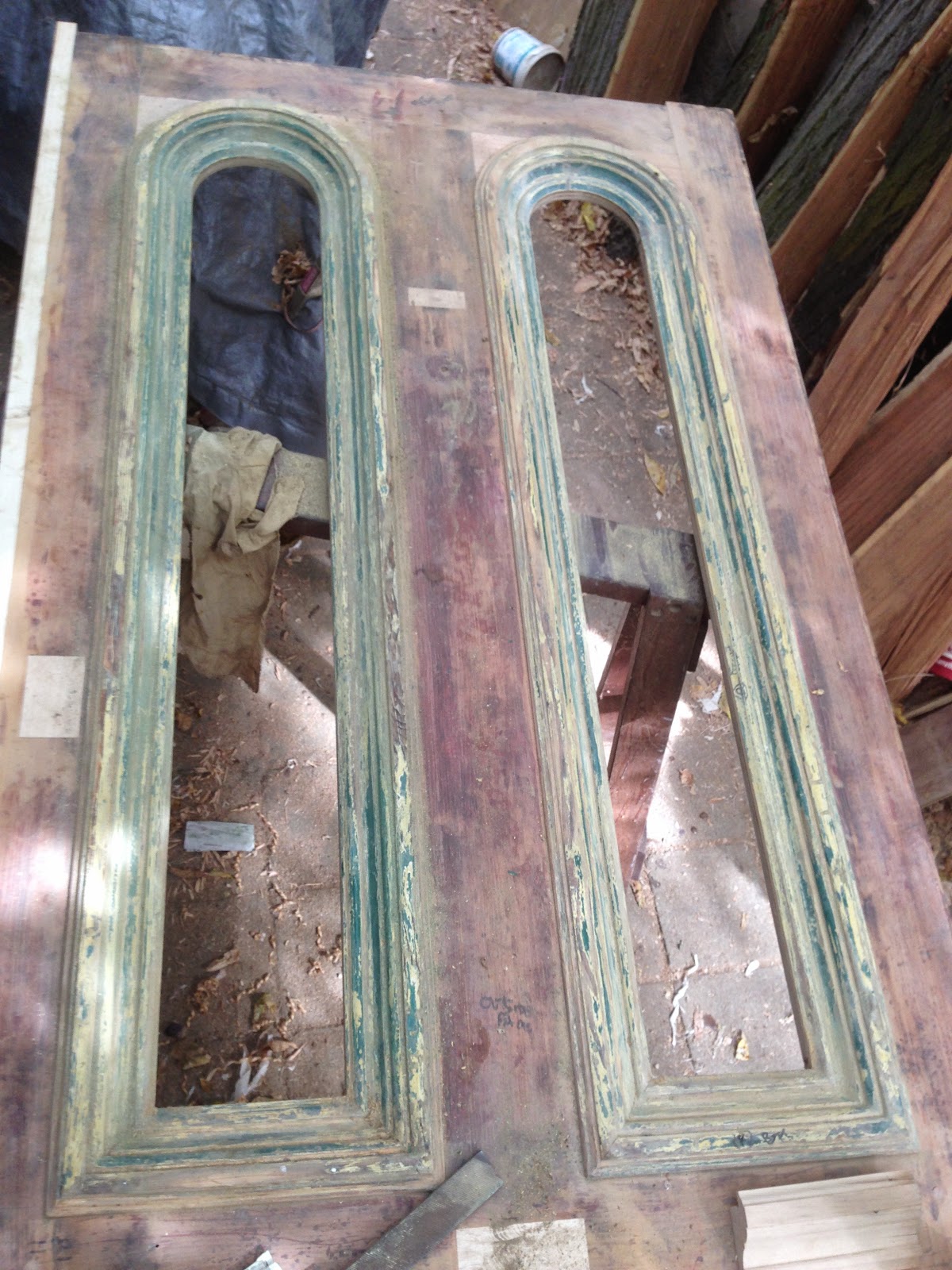 |
Top mouldings fitted and complete on the front side of the door.
Opening flush with the inside edges of the bolection moulding. |
Making and fitting the mouldings on the back side of the door.
With the front side complete, it was time to turn the door over and contemplate the other side.
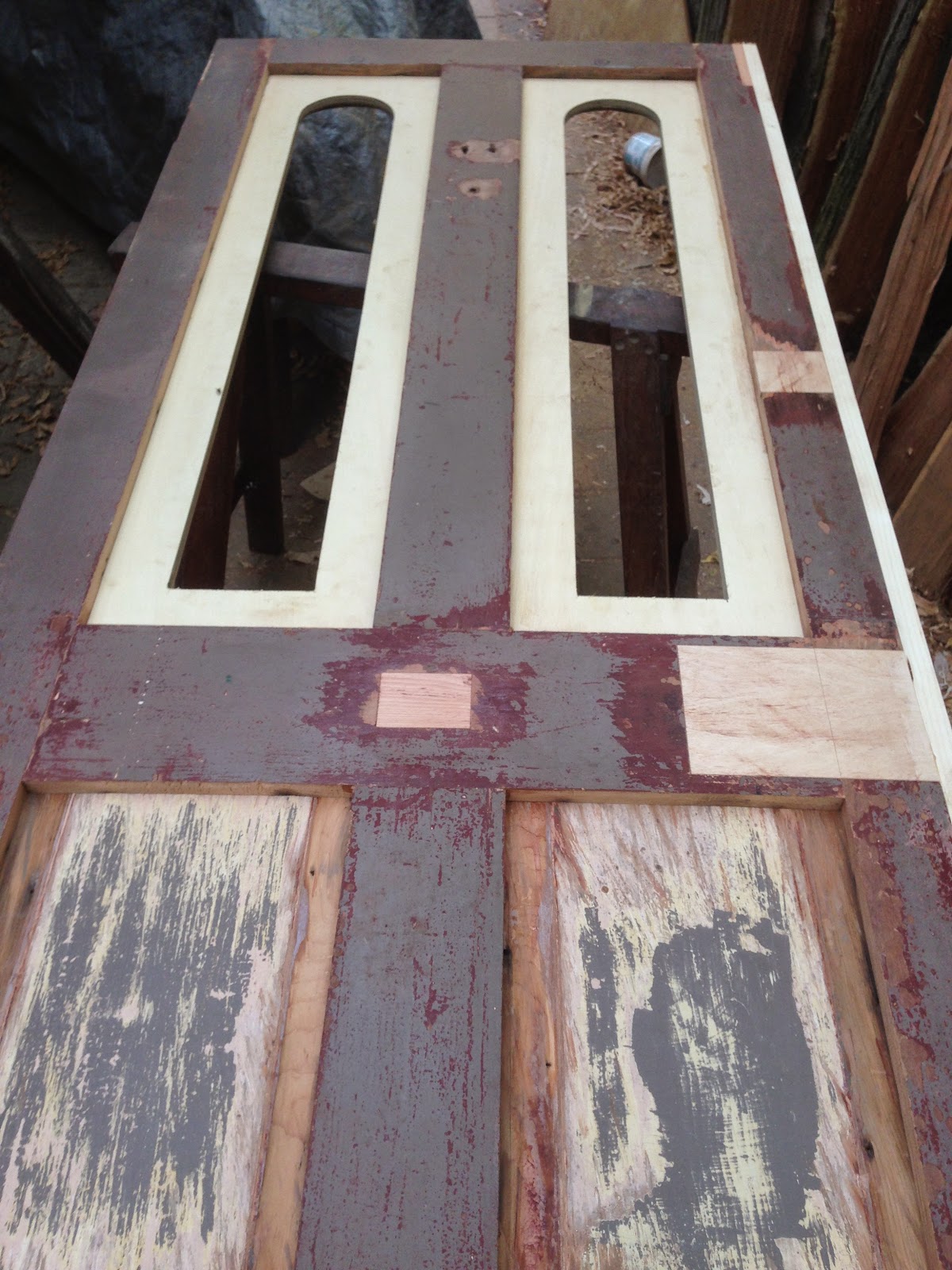 |
Back side of the door, without mouldings. |
The decision was taken to duplicate the big bolection moulds onto the back side of the door, rather than the small original moulding. This would require the making of a heap more of the wide mouldings. I just needed some Oregon or Western Red Cedar...
I learned years ago that old bed frames are a fantastic source of nice close-grained Oregon. I just happened to have the side rails from an ancient bed frame in my timber rack.
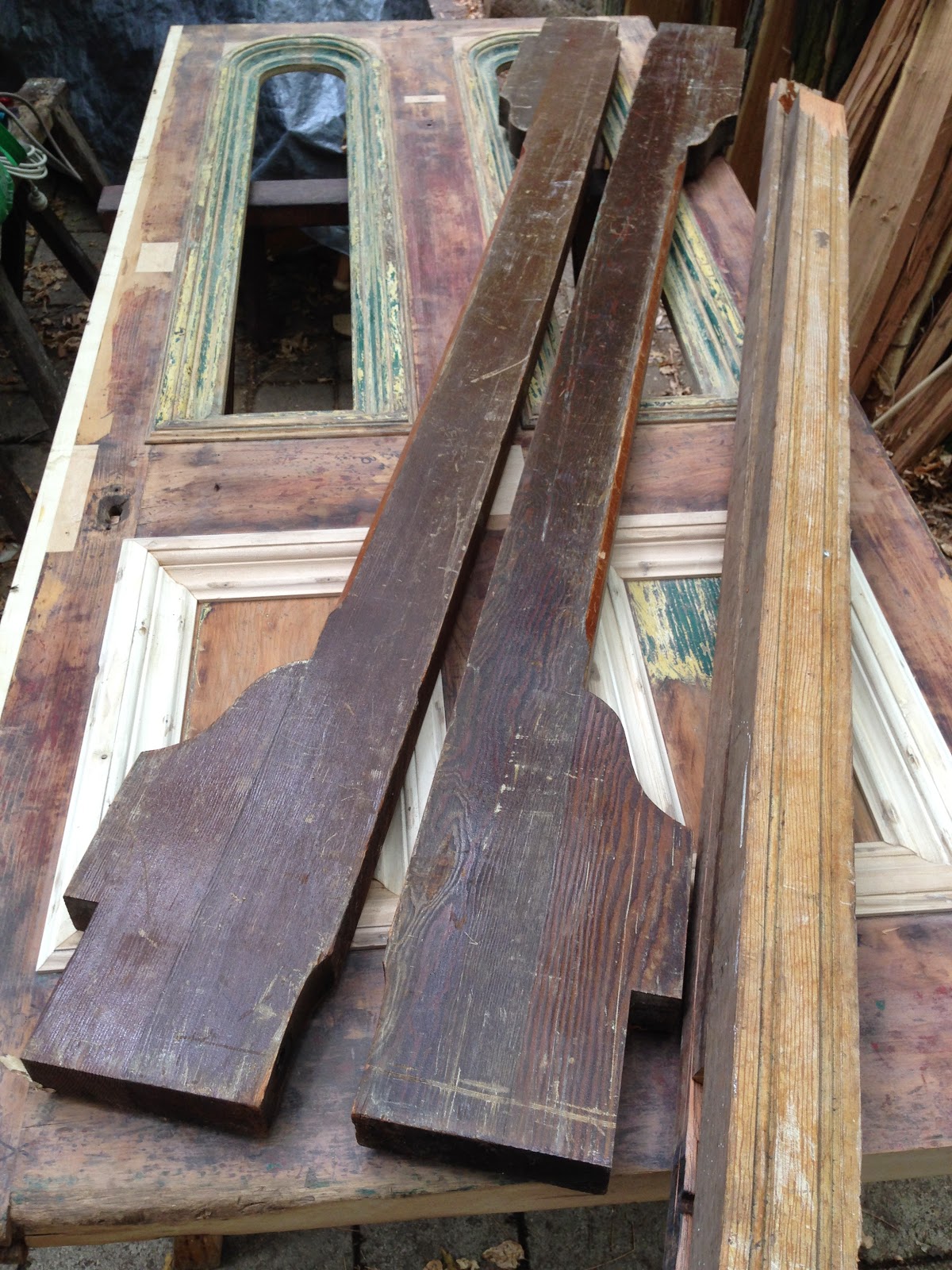 |
The old bed would be recycled to create the new bolection moulds for the back of the door. |
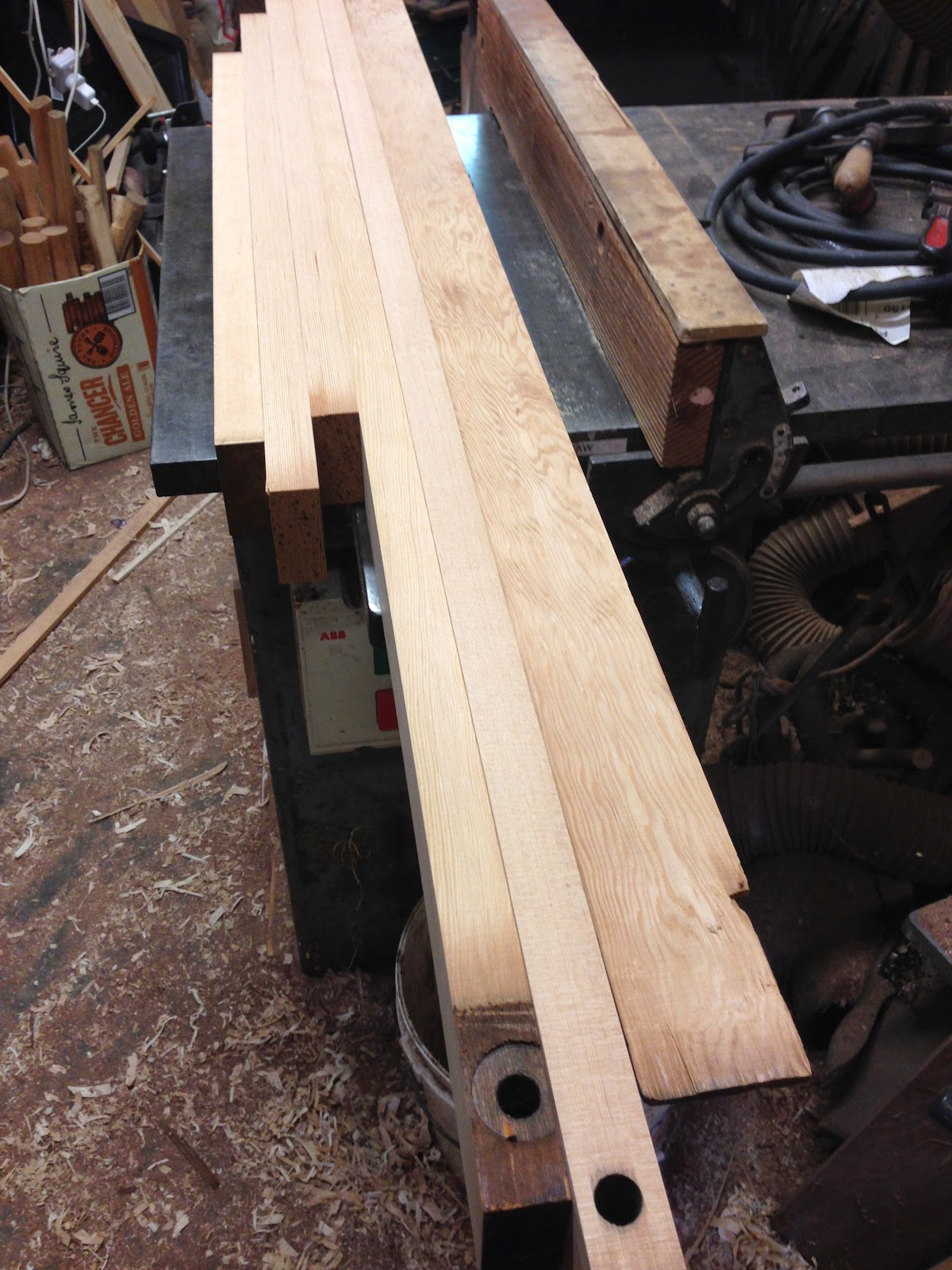 |
Machining up the material from the bed frames. |
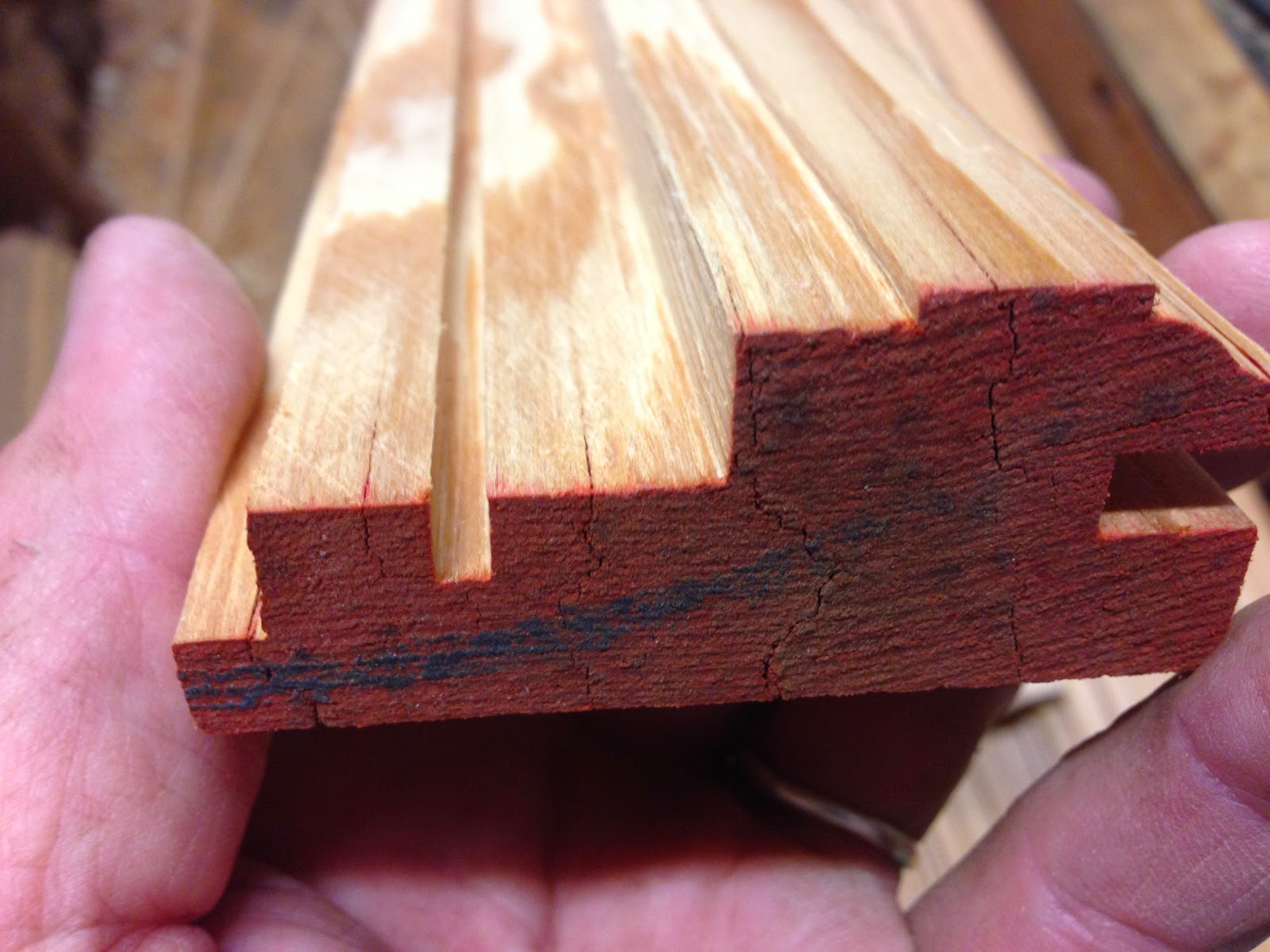 |
Here we go again!! Foundations laid... |
Using the same sequence as before, a new batch of bolection moulding was made from the old bed frame for use on the back side of the door.
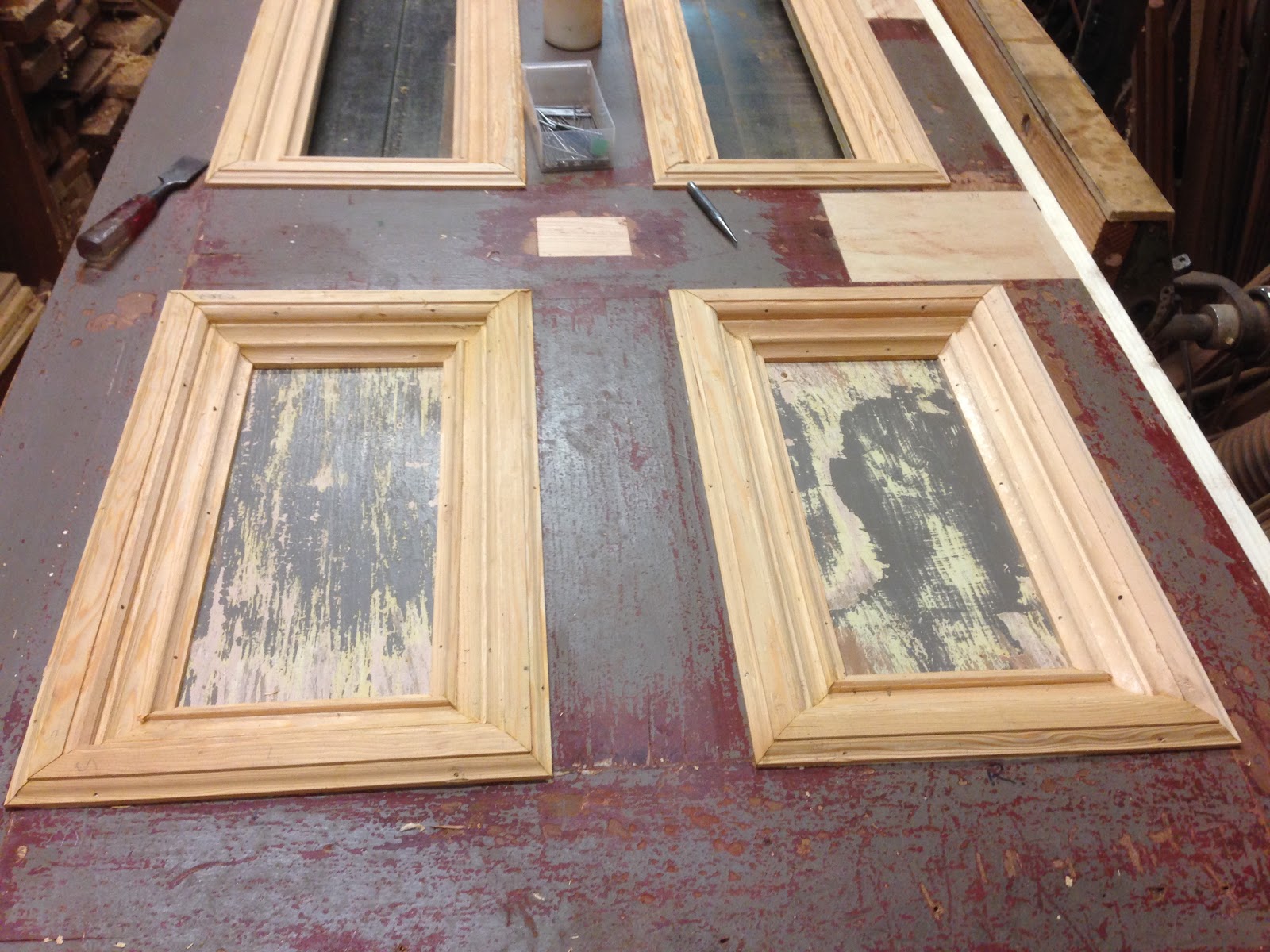 |
The back of the door looks as good as the front. |
The straight sections were easy... but I needed to reproduce the two top curves also. Fortunately, these were each circles each. So I marked these out on two pieces of timber which I screwed together onto a piece of MDF which I then mounted onto a faceplate, which went on the lathe.
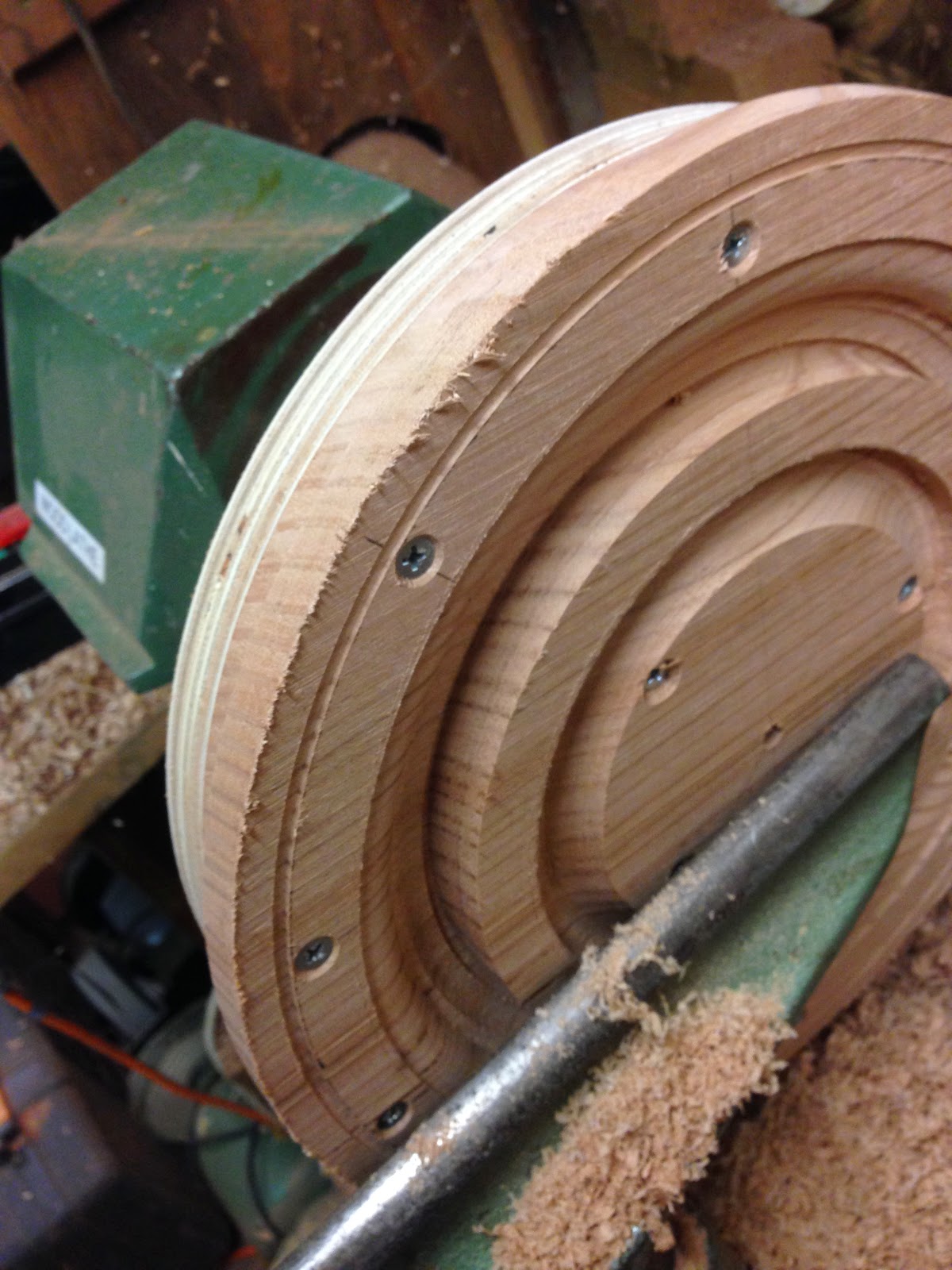 |
Turning the profile on the curved top mouldings. |
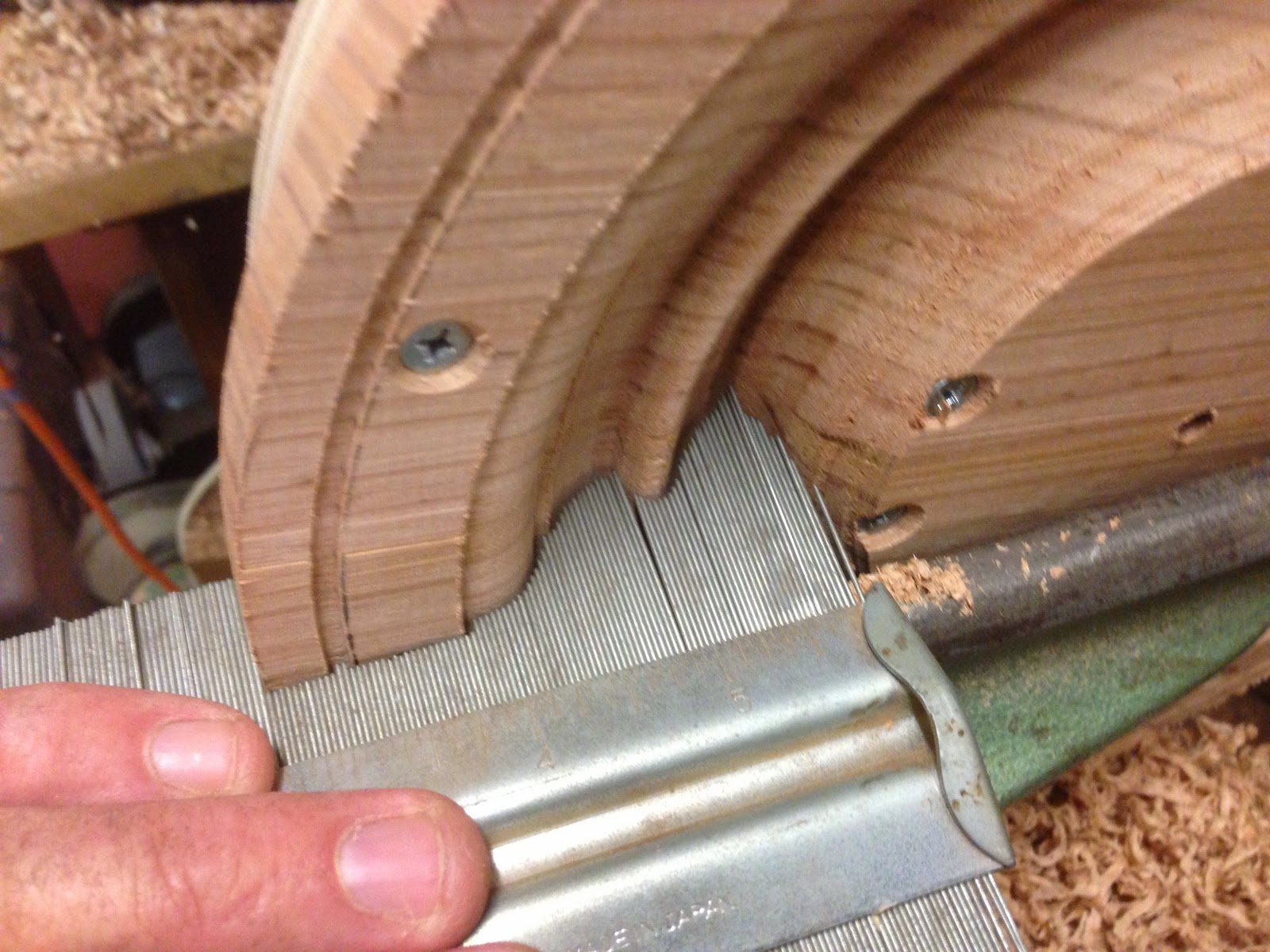 |
Matching the profile with a profile gauge, section by section. |
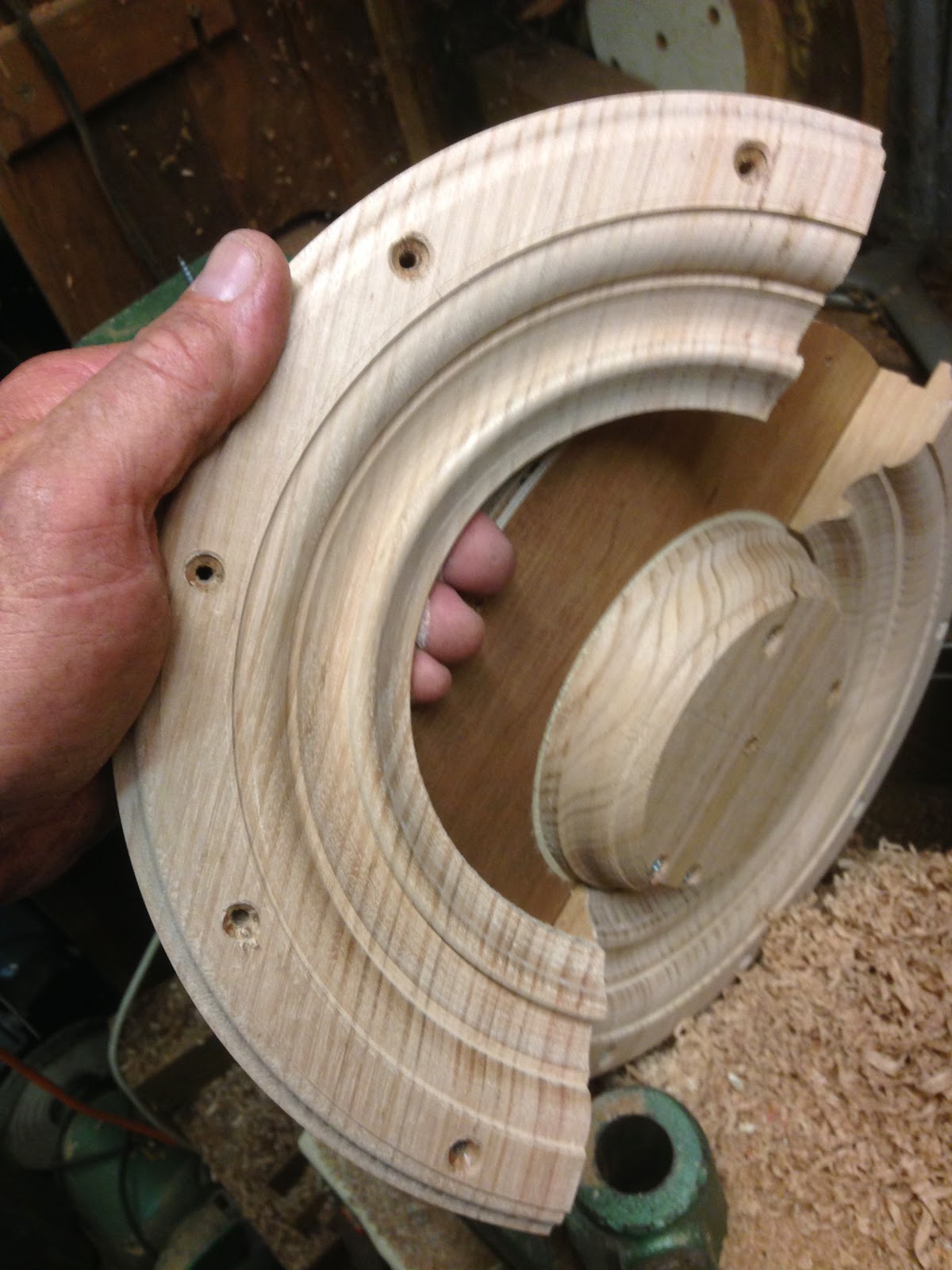 |
One of the two halves. Looking good. |
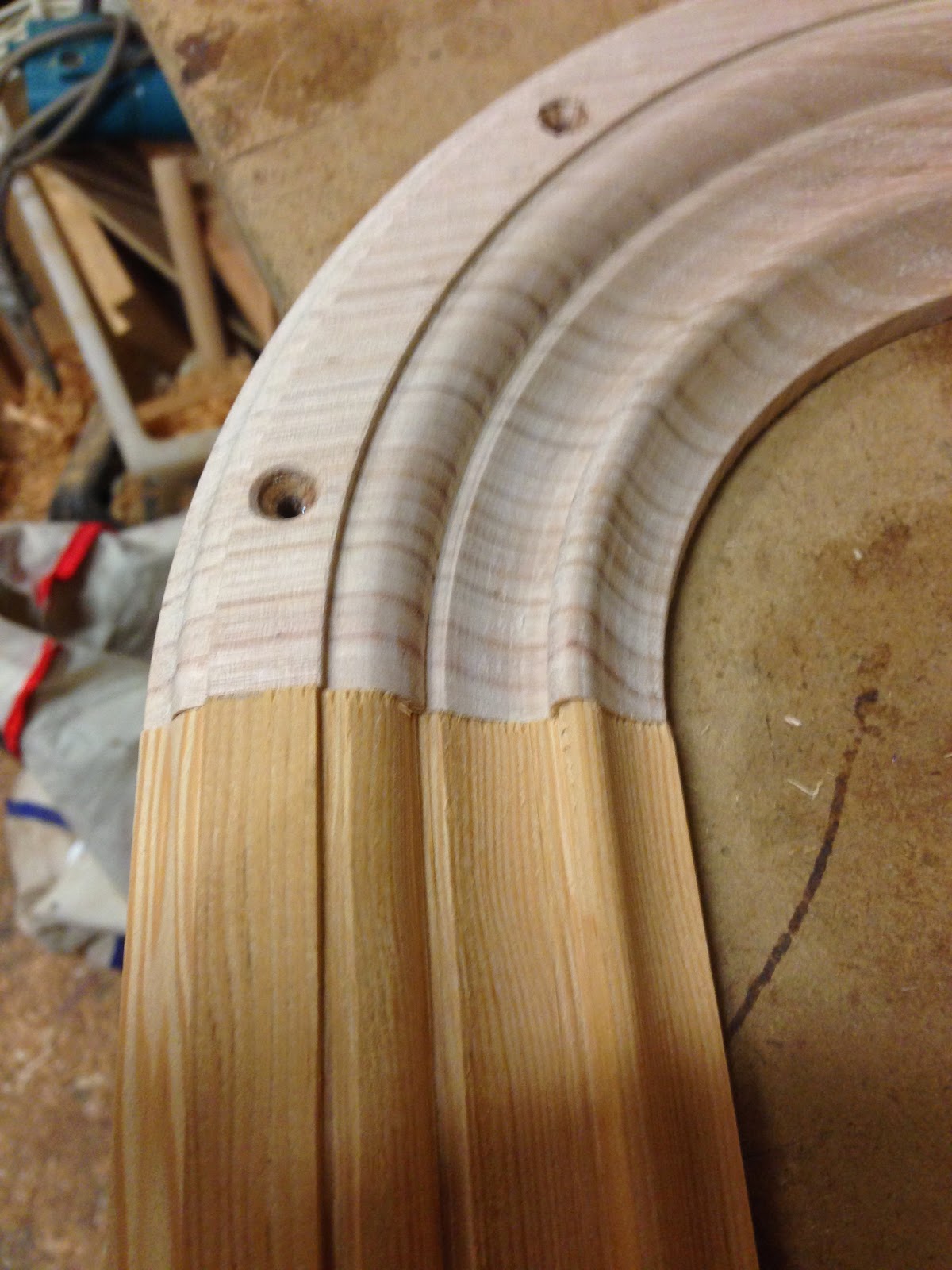 |
A pretty good fit! |
Bring on the leadlight panels!
A 7mm deep x 12mm wide rebate was cut in the back to the marine ply panels to house the leadlights. This meant the leadlights would be housed between the two bolection moulds. Hence the back side mouldings would be screwed on, enabling temporary ply panels to be fitted awaiting the leadlight windows, which had yet to be made.
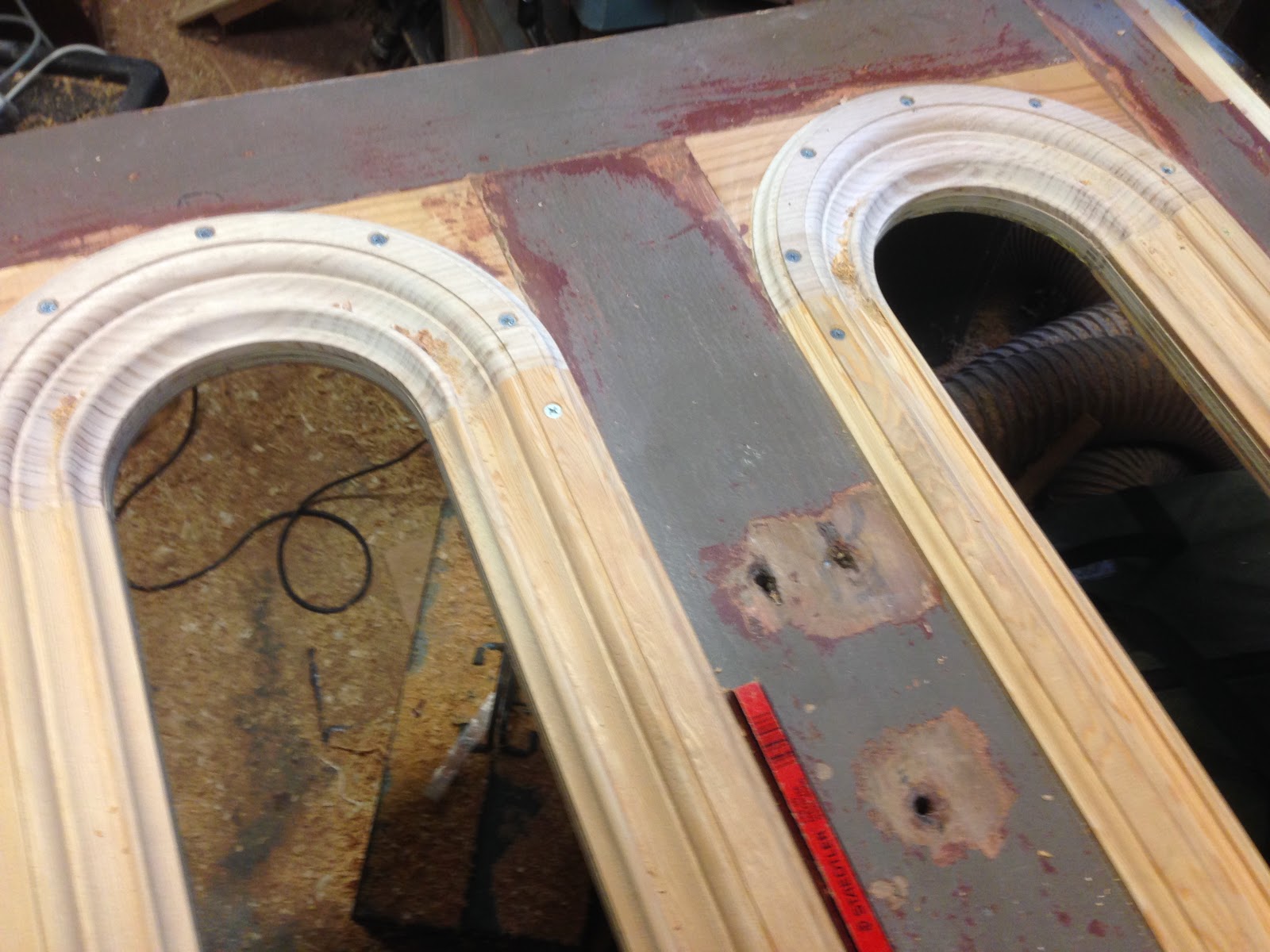 |
Curved mouldings temporarily screwed on. Now the straight sections would be screwed on. |
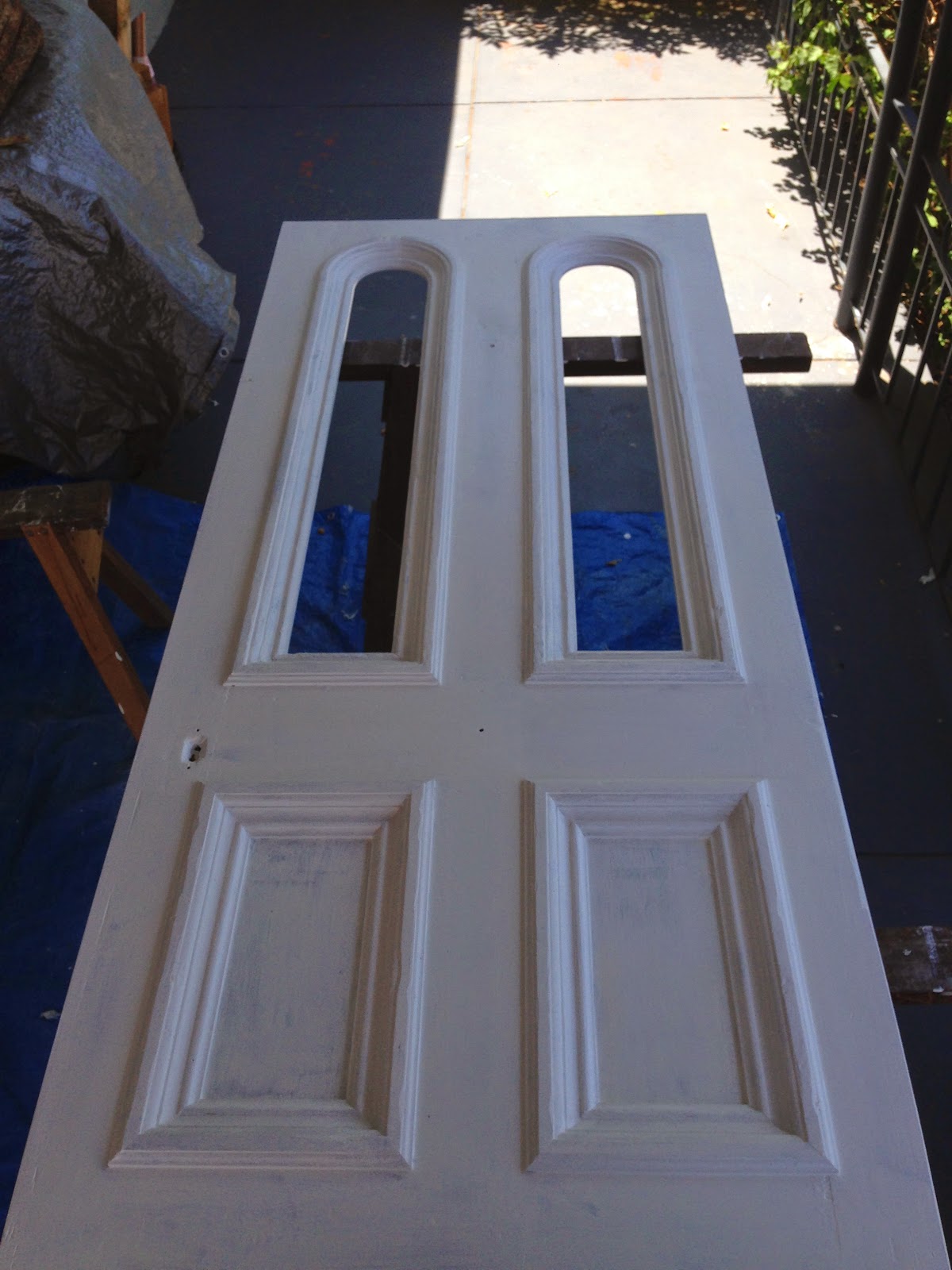 |
First undercoat painted on. Looking good. |
With the mouldings made and fitted, the final cleaning up was undertaken and the first coat or undercoat painted on. Then the temporary 1/4" panels were fitted in where the leadlights would go once made, and another coat of undercoat applied to the door.
The door was then hung, and new lock fitted with much of the old hardware cleaned up and either re-fitted or awaiting the final completion of the door - leadlights, paintjob, etc.
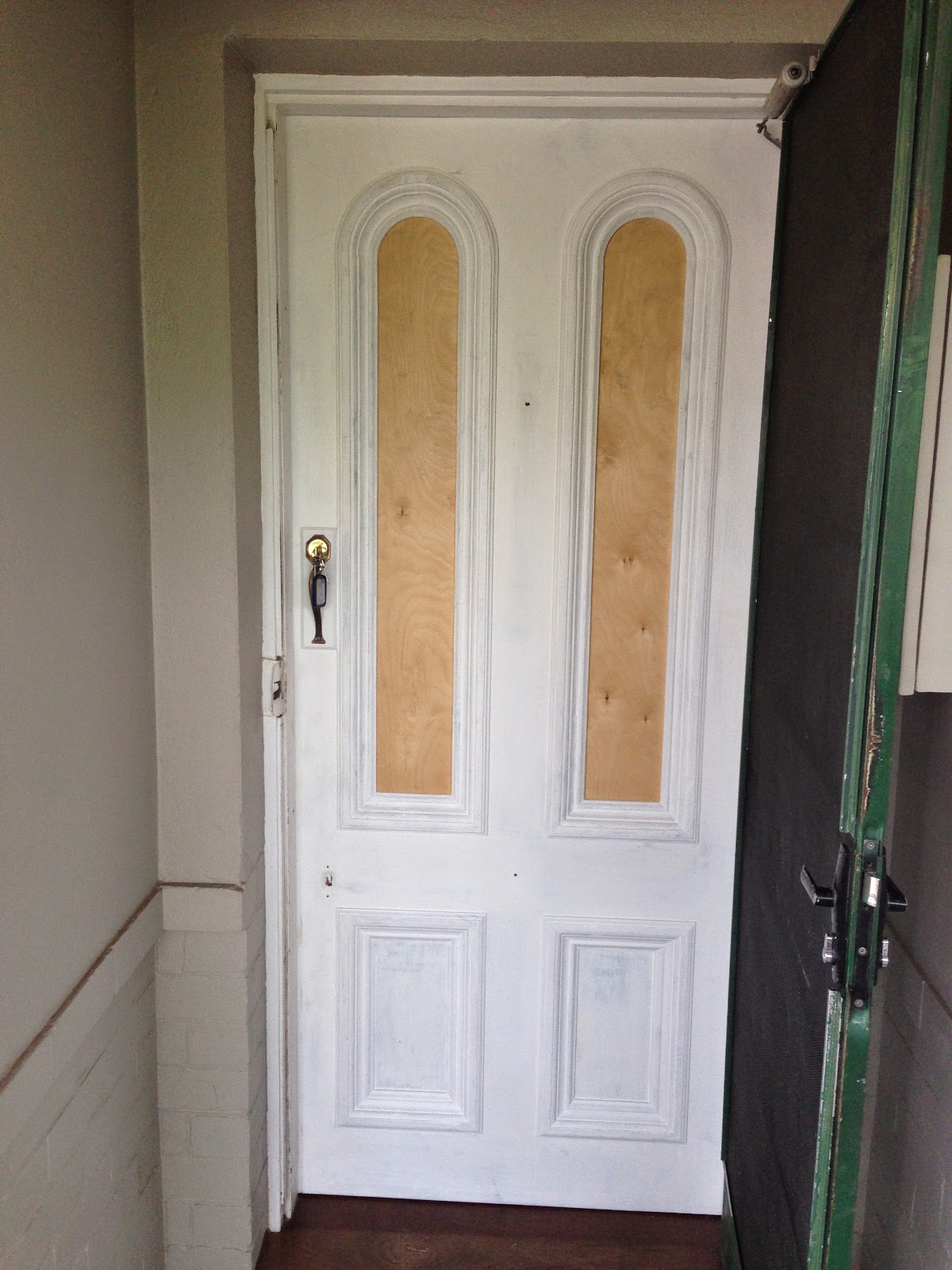 |
The undercoated door, mostly revitalised, modified, and now hung.
Bring on the leadlight panels! |
The only original mouldings, in the top panels on the front side of the door, show signs of a century of use and abuse. So I had "distressed" the new lower front panel mouldings to match. This process involves inflicting deliberate surface damage to the mouldings so that they look like they belong! You have to be careful that you don't overdo it - and that you don't create patterning which is not found in the top section. With the old heavily painted mouldings visually different to the new lower mouldings, I would not know if I got it right until the application of the undercoat to the door. Fortunately, I got it right! That was a relief.
It's been a priviledge to give new life to this lovely old door. Making the mouldings and integrating this into the modification allowing the insertion of leadlight panels was a challenge and a delight. Along the way I often fell like I had met the tradesmen who originally made this door over a century ago. As I carefully pulled the door apart, the tool marks they left behind gave me an insight into their approach and thus their personalities and skills. Now I have left my marks on the door too.
Maybe in another century another tradesperson will be giving this same door new life again... who knows? However I bet they'll never know the material from an old bedframe is now integral to this door! I love the fact that unless it rots or is eaten by insects, wood can be recycled indefinitely. For millenia. Fantastic, eh? This door is living proof of this reality, and stands in stark contrast to our current wasteful throwaway Western culture.
As I worked on this door, I'm sure I could feel the planet smiling...