I have to admit it. I am not a big fan of Marri (Corymbia calophylla) as a furniture timber. Sure, here in Western Australia it is currently the most popular furniture timber in the furniture retail outlets... but that doesn't encourage me to want to use the stuff! However, I had customers who wished their TV cabinet to be made from Marri, so after I was given the go-ahead I was off to the local timber merchant to pick through the racks.
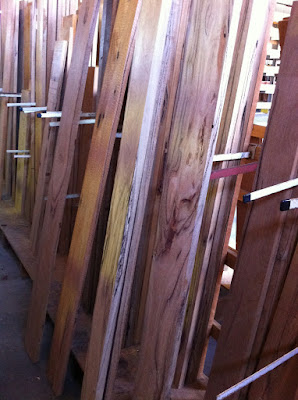 |
Marri timber in the racks. Ex-inch and a half stock here, dressed to 175 x 30mm. |
Selecting the timber for the project.
You have to do a lot of digging in the racks selecting any timber, to get the good stuff - but with Marri there is much more digging to do as there is a lot of rubbish. One of the family of trees knows as Bloodwoods, most Marri is riddled with gum veins (kino). This gives the wood it's feature, but the down side is that much of the gum veins can fall apart and can be structurally unsound.
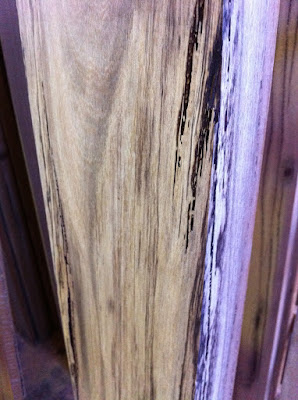 |
That's spalting on the right - in the sapwood. Sapwood also tends to get pinholes from Lyctus borer. |
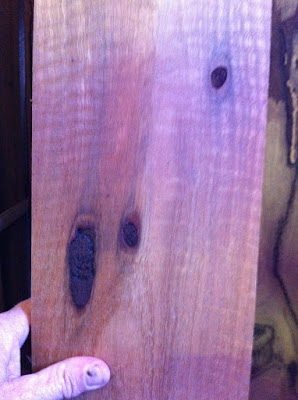 |
Classic big borer holes in Marri, loosely filled with a natural mixture of the larvae's sawdust and excrement. |
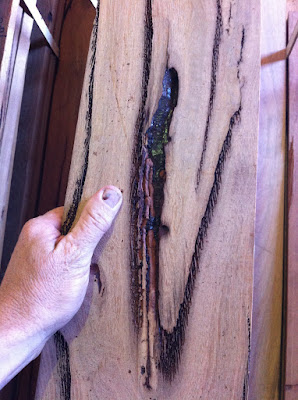 |
Classic rampant Marri gum veins. Too much of this and the integrity of the timber is compromised. |
The common technique used by many furniture manufacturers is to pour black resin into the gaping gum veins. This looks good for a while, but personally I reckon it is not a good practise. It defies our understanding of timber technology. Pouring an inert material into big fissures in the timber, when the timber will move with changes in moisture content, just doesn't seem to make sense. Run your hand across a table top with resin filled chasms, a year of two after the table has been made, and you can feel the raised "speed bumps". On occasions the resin can separate from the timber, which is a real bummer. So my aim was to select timber which had some gum for the feature, but no gaping chasms.
The other challenge selecting timber from the racks is to find sticks which have no wind (propeller twist), almost no bow (bend on the face), and very little spring (bend on the edge). I rejected a lot of boards in the racks to find the few sticks I would purchase!
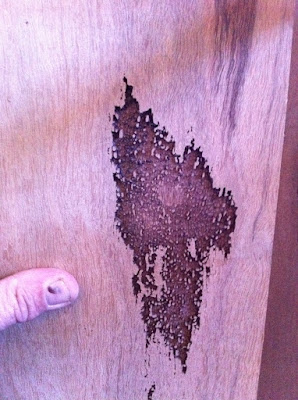 |
Another variation, where bands of gum are parallel to the board's surface. This stuff fritters. |
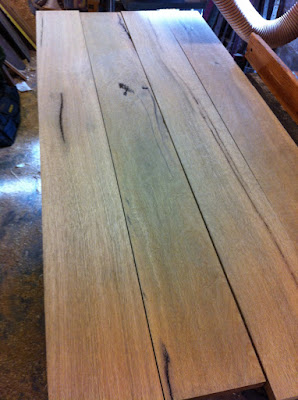 |
The selection process. Board sections are selected, docked oversize, and here laid out to maximise colour matching etc. |
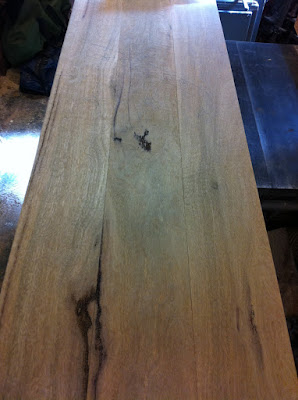 |
Edges have been jointed ready to prepare for gluing up. |
The story of Marri.
It's worth doing a deviation on the story at this stage, for the Marri story is an interesting one.
Endemic to the southwest of Western Australia, Marri grows in a broader range than Jarrah, but commonly in the same territory. Well know for it's characteristic fruit which are often know as Honkey Nuts or Gum Nuts, Marri was until recently lumped under the genus Eucalyptus. The botanists have since shifted all the Bloodwood sub-set into their own genus - Corymbia. Most people still think Marri is a eucalypt. The name Marri is a Nyoongar (local indigenous) name for the tree, which has been adopted as the most common name for the tree. Interestingly the gum (kino) from the tree has many medicinal properties which have been utilised by Nyoongar people for thousands of years. Mature Marri trees are a very significant for food and habitat for a wide range of bird and animal species in the southwest of Western Australia.
Marri is a very hard timber, with interlocking grain. Marri has an air dried (12%) density of 850kg/m3. For readers in the Northern Hemisphere, this compares to European Oak at 720kg/m3 and American White Oak at 760kg/m3. Not good for firewood, as it is hard to split and the burnt gum tends to block up chimneys. The gum veins break down in the elements, so it is not good for external construction. The gum veins hold a lot of loose material, so they can often break down. This can make it unsatisfactory for construction purposes, though it was sometimes used for construction out of the weather, like for rafters, joists and beams. This was not very common.
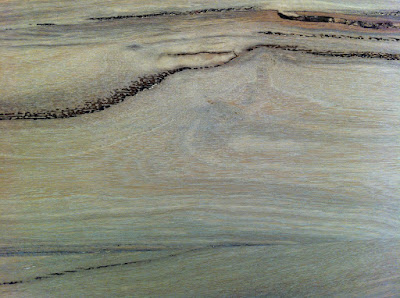 |
Classic Marri timber. |
While a few people had played with Marri as a furniture timber over the years, it came into its own as a furniture material really by chance. Marri was mostly logged for woodchips for the paper pulp industry, from 1976 until 2001. Many millions of tons of these low grade chips were sent to Japan in that period. Every now and then a log would be found that had very few gum veins in it. Only about 1 or 2 logs in every ten are considered suitable as sawlogs, and there is no known reliable way to select these suitable sawlog trees from standing trees in the forest. These suitable logs found via the woodchipping industry were offered to the timber industry for sawlogs. The experimentation took place and gradually a small furniture industry grew up around Marri timber. Time passed, and by 2001 the Japanese wanted a higher grade cleaner greener product, not derived from native hardwood or old growth forests. The transfer across to woodchips from Blue Gum plantations had begun.
The resulting demise of the Marri woodchip industry had a big impact on the Marri furniture industry. The Marri logs available to the furniture industry come from areas of forest being logged for jarrah and karri, so most of the marri sawlogs tend to have lots of gum veins. Hence the use of the black epoxy resin as an effort to do high value adding to what is really a lower value timber than the furniture industry has traditionally used. The popularity of marri furniture is driving this, and the gum veins are the seen as feature in what would otherwise often be a featureless timber.
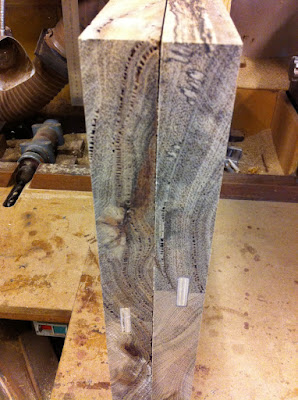 |
End grain of the glued up cabinet ends, showing the gum veins and the plywood tongues used for jointing. |
Interestingly, if it wasn't for the gum veins, Marri would probably be Western Australia's most valuable timber resource, now that jarrah is gradually disappearing from the timber menu, due to reducing logging quotas and our changing climate . With the reducing rainfall over the last 40 years that has beset the Jarrah forest, Jarrahs are just not growing back as they did before. Marri has become an invasive species, growing faster than Jarrahs and surviving in drier conditions. The nature of the jarrah forest is changing, as the climate changes. Of course the changing jarrah forest was already underway due to the logging of the forest for the last 180 years. As a timber of limited value for well over a century, selective logging saw Marri trees left standing in preference for the highly valued Jarrah trees which were felled for sawlogs. The gene pool of higher quality jarrah trees was in this way gradually being reduced as Marri trees increased as a proportion of the forest. In the 1970's, the use of clearfelling coincided with the woodchipping era. Whole areas of jarrah forest were clearfelled with jarrah becoming sawlogs (or later logs destined for the silicon smelter) and the marri logs went off to the woodchip mill, to be chipped for export.
The loss of so many very old mature Marris from the forest during the woodchipping era has reduced the number of habitat trees available for so many of our native birds and mammals who need these hollows for shelter and nesting. Marri trees are very common in our famous wine growing areas of Western Australia. A summer flowering tree, wine growers are keenly aware of the Marri flowering. If the trees flower too late, the hungry Silvereyes (small native birds) will eat the grapes if netting is not used. If the trees flower before the vintage is ready, the birds will mostly leave the grapes alone. Marri flowers are rich in nectar and are an important food source for a great many species of birds, mammals, and insects. In so many ways, Marri is an interesting and important tree in the south west of Western Australia.
Making the cabinet.
After that little diversion, lets get back to the making of the Marri TV Cabinet my customers' had requested.
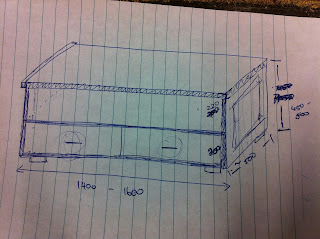 |
All furniture starts with an idea and a function in mind. My customers' initial drawing. |
Simple in design, the cabinet will have a big flat screen TV sitting on top, an open shelf underneath to house DVD players and other bits of media technology, and a pair of drawers under that to house a heap of DVDs and other stuff. Length 1500mm (nearly 5 ft), depth 480mm (19 inches) and height just over 520mm (21inches).
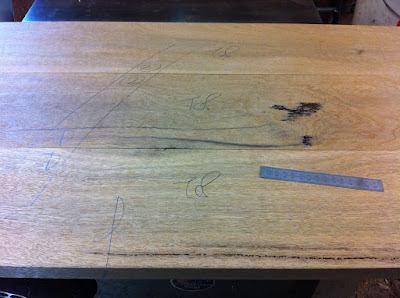 |
With the timber selected and the edges jointed, it was time to prepare for gluing. |
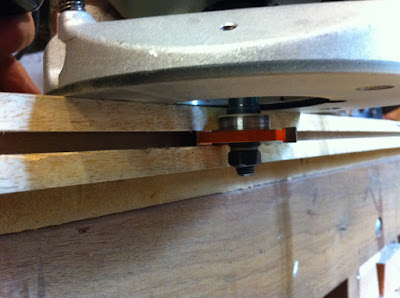 |
A 1/4 inch Slot-cutter bit in the router does a great job cutting the grooves for the plywood tongue. |
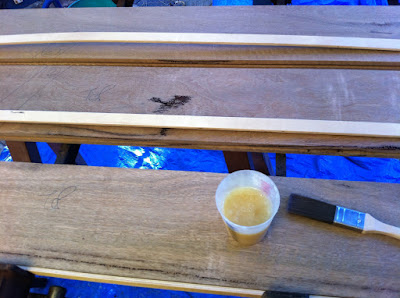 |
Ready to go. The epoxy glue mixed up, the boards and plywood tongues ready, laid out on sash cramps... |
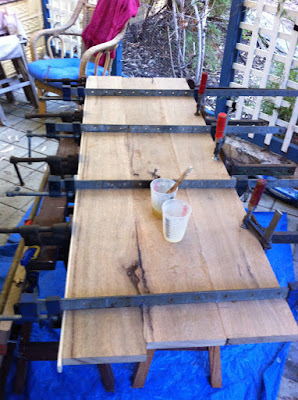 |
The top glued up and cramped to dry overnight. The cabinet ends and mid shelf were done also. |
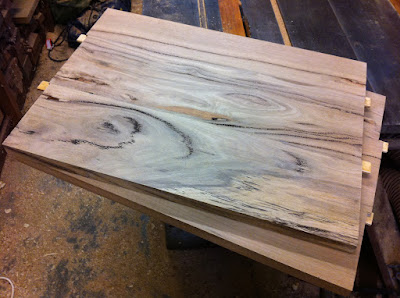 |
The glued up end panels, now sanded. The protruding plywood tongues visible. Still to be dimensioned. |
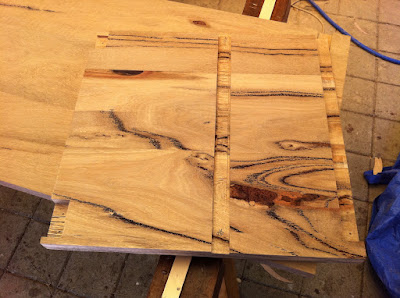 |
Dados, rabbets and housings cut ready for the cabinet clue-up. |
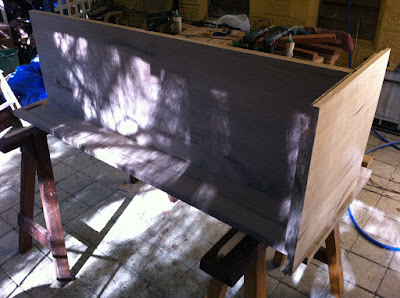 |
The dry fitting in progress, getting ready for the cabinet glue-up. |
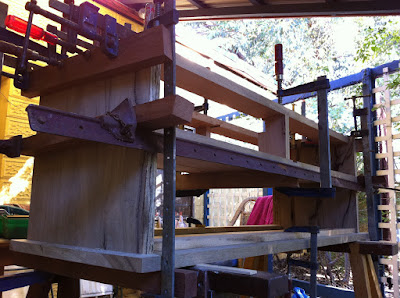 |
The cabinet glued up and in cramps. It was left to dry overnight. |
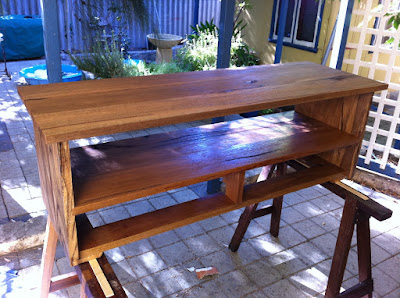 |
First coat of polish applied after the necessary sanding and preparation. |
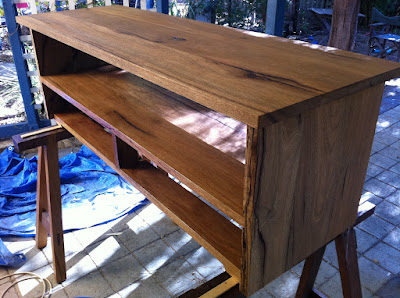 |
While the polish was drying, it was time to get on with making the drawers and the backing boards. |
Cutting the dovetails for the drawers.
I always cut my dovetails by hand. I have done it enough over the years to do it quickly and accurately. Most of the time they come together with a nice snug fit, with no need to muck around paring and trimming to make them fit. However, it is still always a great source of satisfaction when that clean snug fit takes place on the first run!
Having prepared the timber based on the dimensions of the drawer, the scribe lines are made and the tails are planned and marked out. Doing it tails first enables the saw cuts to take place through the whole stack of 4 drawer sides simultaneously. The stack is separated and the chopping out of the waste is done.
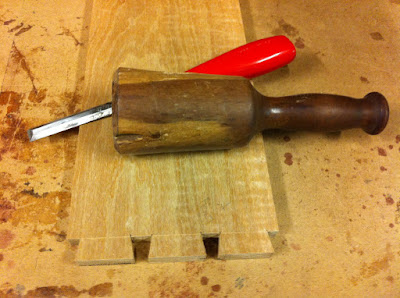 |
My trusty mallet and a bevel-edged Footprint chisels do their magic, chopping out the waste to form the tails. |
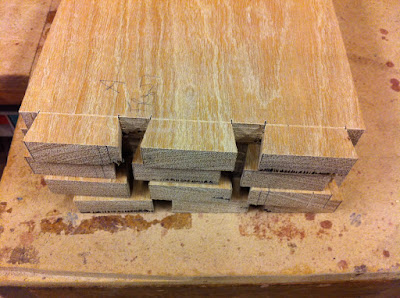 |
The stack of drawer sides ready to mark out the pins. |
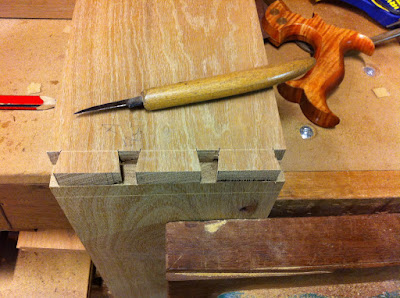 |
Marking out the pins.Carefully lay the side in position and use marking knife to mark the pin positions. |
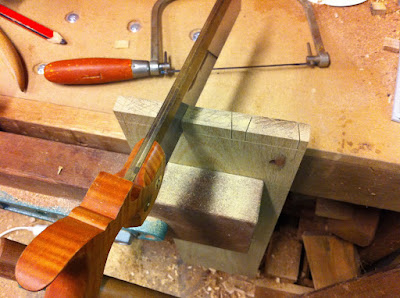 |
Cutting the sides of the pins - on the WASTE SIDE of the scribed lines. |
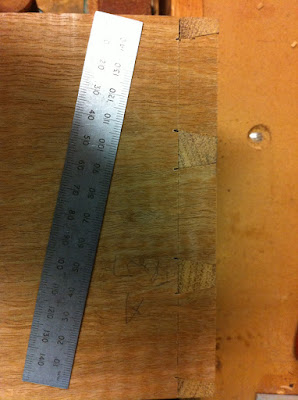 |
It's a nice fit first go... you beaudy! |
With the dovetails cut for the joints on the front of the drawer boxes, it was time to make the rest of the drawer components. There are a variety of methods used for the rear joints of drawer boxes. The method I used here was to house the back into dados near the rear of the drawer sides. The drawer base is housed into a groove half an inch above the inside base of the sides and the front. The drawer base is housed into the groove on those three sides, and is fixed onto the underside of the drawer back. The drawer base was made up from tongue and grooved boards I made up from off-cuts, running across-ways. All in all a pretty standard way of making drawers, old school. The difference here though was that my customers wanted the drawers mounted on metal self-closing drawer runners. These do have a very nice action! I was in a bit of a rush, so finished making the drawers without taking any photos. Unfortunately, I forgot all about it at the time...
Putting it all together.
After careful selection of timber, I was able to make up the most wonderful pair of drawer fronts from a few nice sticks I had dug up for the purpose from the racks at the timber merchants. Machining Marri is always interesting, as the pattern and nature of the gum veins changes as your remove each layer through the thicknesser. I was very happy with the result I was able to obtain. Lucky!
With the drawers made, and the drawer fronts too, it was time to fit the drawers. In this case I did the fitting first, and then removed the runners from the drawers and polished the drawers. I also cut finger grips under the drawer fronts, in case my customers agreed with me that the drawer fronts would look better without the metal handles they had talked about. They did agree, too.
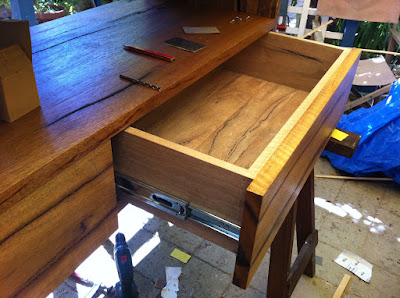 |
Drawers fitted on the runners, drawer fronts fitted to the drawers. Time to polish the drawers. |
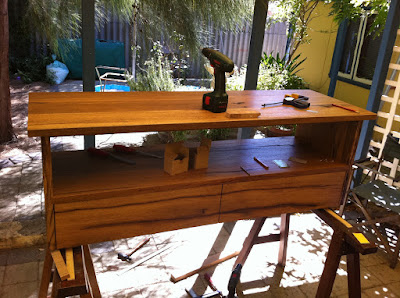 |
How's those drawer fronts! Very nice indeed. |
Other than the final waxing of the whole cabinet, the last task to be done to complete the cabinet was to fit the back. For this I used V-joint Marri lining board, purchased from the timber merchant. At 8mm thick, it has a 65mm cover. I often make my own lining board, but the material available was OK for quality. I had docked the pieces to length and polished them, them cut some holes for cables and ventilation.
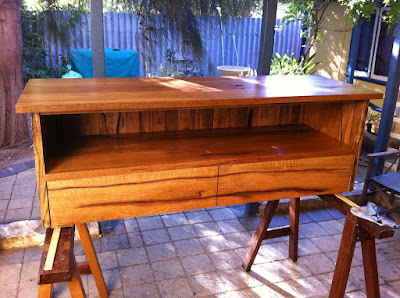 |
The finished piece of furniture, ready for delivery. |
I arranged delivery to my customers' home, and their process of transferring the media technology from the old TV cabinet to the new one began. A serious amount of cable spaghetti! Standing before the TV cabinet is an older large Marri coffee table. They fit together well.
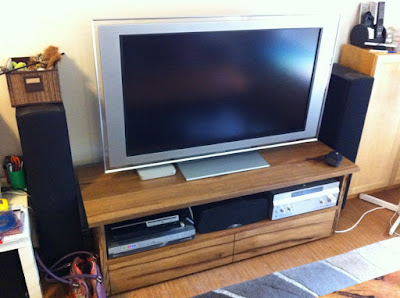 |
The new cabinet fulfills its purpose. |
Another job done, and some more happy customers.
I commenced this blog post admitting that I was not a big fan of Marri as a furniture timber. However, I have to say I did enjoy working with the stuff on this particular project. It was a nice change, and the hardness of the timber did make the dovetailing very easy. You can saw, chop and pare nice clean sharp elements of the joinery with a timber like this using sharp hand tools - so long as you avoid the gum veins. The most important thing of note from making this piece was the reminder that a lot more time needs to be spent working with Marri, being careful about gum vein quality and placement, and selecting the right stick for the right application. Did I use any filler or black resin in this piece of furniture? Nope. None at all. It took the couple of coats of the oil/varnish mix well, and the nice wax coating at the end made it silky smooth. A simple design, but a nice and functional piece of furniture. Thankyou, Corymbia calophylla.